●水野氏の3Dプリンタ遍歴
2013年~「CubeX」導入当時の価格約35万円
2015年~現在「AFINIA H480」導入当時の価格約20万円
2015年~現在「Atom 2.0(日本名Maestro 3D printer)」導入当時の価格約25万円
※体感上の比較
プリントの速さ(体感) CubeXを[1]とした場合、AFINIA [3]、Atom [5]
プリント性能(体感) CubeXを[1]とした場合、AFINIA [5]、Atom [8]
・3Dデザインツール
Rhinoceros 5.0 / CATIA V5
・はじめに
僕自身の3Dプリンタの経験を率直に書きました。3D関連で紹介していただくことが多く、3D操作に長けている人と思われがちなのですが実際はそうでもなく、仕事の最終段階やスケッチだけでは表現が難しいとろは3Dを使っている程度で、ほとんどはアナログ的に創作をしています。
普段は依頼をいただいてデザインをしているため、依頼製品について僕自身があまり表に出ることはないのですが、デザイン会社代表としてのPRと、デザイナーとしての自己表現のために自主作品を年に2作のペースで制作して発表しています。結果として3Dデザインの鍛錬にもなっています。テーマとしては「オモシロソウ」と感じてもらえる作品になるように心がけています。また昨今は「これは商品化するの?」と思われることをテーマにユーモラスな作品制作をしています。ニッチではありますが、もしかしたら製品化していく作品もあるかもしれません。
そんな個人デザイナーな僕に3Dデータのアナログ的可能性を考えさせてくれた3Dプリンタは、はたして魔法の箱だったのか? このコラムが、個人デザイナーで3Dプリンタ導入を考えている方の参考になったり、すでに導入している方に共感いただけたら嬉しく思います。
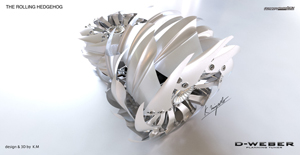
▲オリジナル作品「ローリングヘッジホッグ」 ハリネズミとタイヤをモチーフにしたオブジェ。(クリックで拡大) |
|
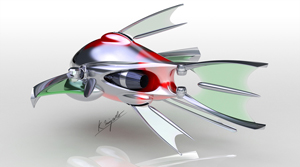
▲オリジナル作品「ジェット金魚」 清涼感ある機械をテーマにした、優雅に泳ぐメカ金魚。
(クリックで拡大) |
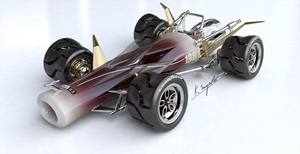
▲オリジナル作品「ちくわレーシング」 竹輪をモチーフにしたレーシングカーテイストのオブジェ。(クリックで拡大) |
|
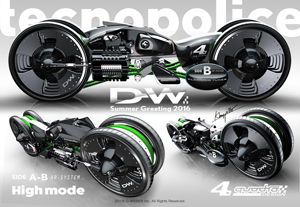
▲オリジナル作品「テクノポリス」 カセットデッキから連想してデザインしたモーターサイクル。(クリックで拡大)
|
・3Dプリンタとの出会い
2013年のある日、「3Dプリンタが家電量販店で買える」というニュースを聞いた。「CubeX」だ。加工屋さんや木型屋さん 金型屋さんにお願いしていたコトがデスクの隣にやってくると考えるとゾクゾクしたことを思い出す。3Dプリンタを見たい! 展示が開始されたと同時に東京の家電量販店まで足を運び、店員さんに質問をしまくり、ほぼ即決で予約を決めた。
正直なところはどんなものであっても最初から買うつもりで東京まで行ったのだけれども、店頭にあったソレが作る造形物は、僕の思い浮かべていたモノとは遠く違っていたし、なによりも「コレはナニに使えるのだろうか?」というハテナを自分の中で消化するために少々時間が必要だったが、店員さんに質問しながら「まずは始めろ!」と心の中で自分の尻を叩いた。
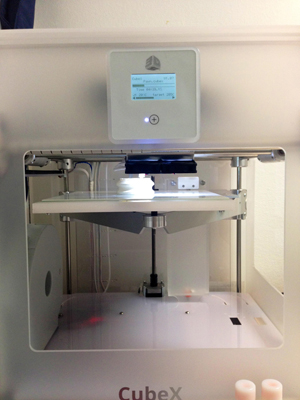
▲CubeXでサンプルをテスト出力中の様子。当時は出力にかなりの時間が必要だった。
(クリックで拡大) |
|
|
・3Dプリンタのファーストインプレッション
予約から2ヵ月後、僕にとって初めての3Dプリンタがやってきた。今まで画面の中でしか表現できなかった自分の作品を、これからは自分自身で出力することができるのだ。これは凄い革命的なことだ。3D CADが個人事業レベルでも導入できるようになった頃のことを覚えているだろうか? その時の感覚に近い期待と喜びがあった。というよりも過去にこんな「家電」が存在していなかったのだから、大げさに言うと「これからスゴイことができてしまう」と喜び勇んだ。
「何を出力して試そうかな」とウキウキしながら、巨大な箱を開け、設置はあっけなく終了。問題は設定だった。個人レベルで購入できるとはいえ元は海外の聞きなれないメーカーの製品、マニュアルも専門的な言葉が多く戸惑った。自作PCなどが好きな人には逆に嬉しいかもしれないが、家電感覚で使いたい自分には少しハードルが高く思えてきた。ただ、さすが大手家電量販店の専売だけのことはあり、電話サポート制度を利用してなんとか初期設定までは完了できた。この辺りは「家電メーカー感覚でサポートが受けられること」を期待して決めたこともあり、コレに決めて良かったと心底思った。
まずはウォーミングアップ。お試しプリント用のデータを試すことにした。記憶が曖昧だが、たしか螺旋階段の入ったタワーだった。サイズはチェスの駒くらいか。ハヤル気持ちを抑えながらデータの入ったUSBメモリをプリンタに差し込み、英語表示の操作画面を確かめながらスタートボタンを押した。
「ウィーン、ゴゴゴゴ」と思っていたよりも大きな音を奏でながらソレは動きだした。長かった、予約してからスタートボタンを押すこの瞬間までが本当に長く感じた。親しいクライアントや知人友人に「3Dプリンタ、予約した!」と公言していたのもあるが、とにかく新型車の納車待ちのように長く感じた。そして数時間後、見事にそこにはタワーが完成されていた。家電量販店に展示されていたサンプルとまったく同じだ。「おースゴイ!」と一瞬だけ叫んだ。そして思った「これを作るのが目的じゃない。ここからが本番だ」。
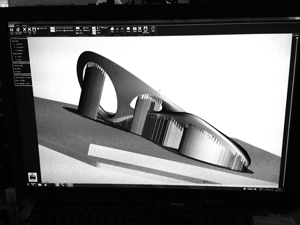
▲CubeX 専用ソフトでGコードを制作している様子。ギザギザの柱のようなものがサポート部分で自動で形成される。(クリックで拡大) |
|
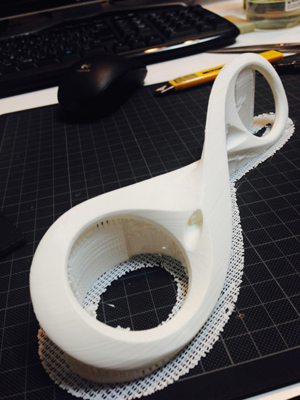
▲実際に出力された作品。バーチャルがリアルに出力されることは当時としては画期的だった。(クリックで拡大) |
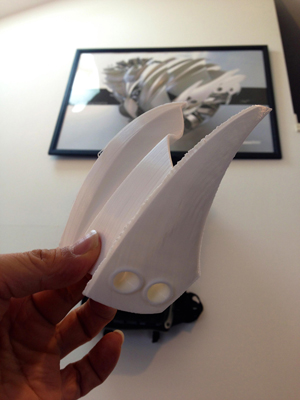
▲CGグラフィック作品と、出力した造形物を見比べる。幸せな瞬間。(クリックで拡大) |
|
|
・実際に自分の作品をプリントしてみて
起業して以来、年賀状とサマーカードのタイミングで3D作品を発表していた。その中から、まずはシンプルな作品から試してみようと決めた。ここでさっそく壁にぶち当たり、以後の作品作りで心がけることになった出来事がある。「厚み」だ。グラフィック用で作った3Dデザインなので厚みなんて作っていなかった。それまでの僕の作品は、たくさんのサーフェスを好き勝手に配置して、組み上げのことなど考えていなかった。グラフィック用途なので困ることもなかったし、第一に自己表現の作品作りだったので誰も困ることはなかった。
予想はしてはいたもののサーフェスモデラーで厚みを付けていくことは結構な作業で、設計的な細やかな工夫も必要で心が折れかけた。「デザインの段階で厚みとアッセンブリーを考慮して作っておけばよかった」。大きな教訓となった。
とにかく自分で作った3D作品をプリントしたい思いで、なんとかメインとなる部分に厚み形状を作り込み、STL出力、いわゆるソリッド化を行う。このソリッド化がまたしても僕を苦しめた。
サーフェスデータを結合するだけなのだが、そこに情や感性なんて言葉は存在せず、クールにドライに「完全に閉じることができません」と警告をいただくこともシバシバ。どこか開いていたのか? もしくはサーフェスが重なっているのか? アタリをつけて修正を繰り返すことになった。完全なソリッドに無事に完成した時でさえメッシュの入り方がちぐはぐしてプリント結果にも影響してきてしまう。多くのデザイナーはサーフェスモデラーをメインに使っていると思うので、この部分で苦労した人も少なくないだろう。
後日談になるが、僕はRhinocerosを主に使っているのだが、STL出力をする前にメッシュ化する方法を覚えた。こうすることでメッシュをある程度目視してから整理できるからだ。何度も出力を経験して「勘」を身に付けていくしかない。ソッドの知識は3Dプリントに限らず「実体化」するために最小限は持っておいた方がよいと思った。
話を元に戻そう。STL化したデータを専用ソフトでGコード(工作機械用のプログラミングコード)に変換して、スタートボタンを押した。「いよいよだ!」。予測完成時間は8時間後。先は長いようではあるが、目の前で少しずつ積層されていく作品から目が離せなかった。2時間を過ぎたころからようやくカタチが見えてきた。「ついに自分の作品がPCから飛び出してきた!」気持ちは高まる。そしてほぼすべての工程を見守ってしまったのである。
完成までずっと眺めていたから、出来上がった時の感動はあまりなかったのが正直なところだ。そして途中から思っていたことがある、「こんなに面質が粗いのか?」「設定を間違えたのか?」「途中で止めてやり直そうか」ということだ。
先進的なものに過度な期待はツキモノなのだが、サンプルはあんなにキレイにできるのに、実用ではこんなに差があるものなのか。仕上がりは良いとも悪いとも言えない、そもそも比べるものもない、NC削り出しのモデルメーカー品と比べるのは余りに差があり過ぎる。ではなぜ結果がこうなのだろうか。答えは簡単だった。問題は自分のスキルとノウハウが足りないからだった。
サンプルはこのプリンタで最上の結果が得られるように開発者が練って練って考え抜かれた造形とGコードを提供しているのに対して、ユーザーは自分の出力したいデータに対して1回のトライで結果が得られると考えてしまう。言い換えれば「速い車を買ったから自分も速く走れる」と思い込んでしまっていた。
マニュアルもあり初期設定のサポートもある、サンプルも出力できた、自分は魔法の箱を手に入れたという気持ちが強く、でも実際は扱う側の技量がかなり必要な「機械」であることを改めて思い知らされた。「これは習得するまでに時間がかかるな」という気持ちと同時に「うたい文句に偽りアリだな」というのが当時の本音だった。ただ それでもやっぱり粗いとはいえ目の前にカタチとなって表れた作品に心が高揚したことは初めての感覚だった。未来がやってきたのは間違いないのである。
・新たな3Dプリンタとの出会い
それからしばらくは、なんとか習得しようとやっきになってトライを繰り返していたのだが、作品作りにばかり時間を割いてはいられないのも個人事業の辛いところで、気が付けば半年以上使わない日々が続き、最後に稼働させた時にトーチ(素材を流し出す先端)に 材料がまとわりついて空中プリントをしつづけたことにより(いわゆるソバ状態)、配線を引き裂いてしまい動かなくなってしまった。
残念ではあったが実はそこまでショックではなかった、というのもその頃には3Dプリンタに対して冷やかな気持ちになっていたからだ。材料も安くもなく、トラブルも多かったし、なによりも思っていたよりもキレイに作れないからだ。サポート部分も剥がすのが大変で、これに時間を使いたいと思えないようになっていたからだ。ただ、CubeXのことを誤解してもらいたくないのが あくまで当時は「最先端のコンシュマー向けマシンだった」ということは触れておきたい。3Dプリンタを個人レベルに普及させた先駆けの機種であり、じっくり習得して使用している人も多々いただろう。
それから1年くらい経った2015年初頭、3Dプリンタを取り扱うメーカーも増えていたが、相変わらず冷やかな気持ちで導入など考えもしないようになっていた頃だ。CADメーカーのセミナーに招待いただいた時だったと思う。とある著名な個人デザイナーさんが登壇された際に「デザインしたモデルを3Dプリンタで検討している。出力時間も速く、サポート部分もパリパリと剥がれるんですよ、この3Dプリンタは」と、まさに目からウロコだった。
こういったノウハウや秘密にしておきたい技術をオープンに開示される方はどんなジャンルでも多くない、とても有難いことだ。「こうしてはいられない!」今まで冬眠していた3Dプリンタへの気持ちが沸々と湧き上がり、帰りの新幹線でスマホから同機を注文、2日後には事務所にそれがやってきた。AFINIAだ。
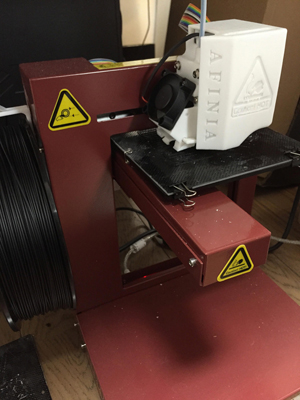
▲素っ気ない見た目とは裏腹に安定した出力結果を与えてくれる。(クリックで拡大) |
|
|
デザイナーさんも登壇で言われていた通り「限りなく小柄でシンプル、まさかコレが?」決してオシャレとはいえないその見た目が逆に「中身で勝負」と語りかけているようだった。驚くほど設定は簡単、専用ソフトも日本語で分かりやすい。まずは前機で断念した作品を出してみよう。専用ソフトでデフォルト設定のままとりあえず試す。前機ではPLAを推奨されていたがAFINIAに付属の材料はABSだった。ベットに熱が入るヒートベット方式で一層目をしっかりとベットに固定できることもありがたい。さて、PCをつないで稼働しはじめたAFINIA、ABSの溶ける匂いは予想以上にキツイが想定はしていたことだ、問題ない。プリントはスコぶる速い。僕にとっては2台目の3Dプリンタだ、あれから2年も経っているし、技術の進化はあって当たり前と考えていたが、実際にはウキウキでたまらなかった。そして2時間後に出現した立体物は、過去にないくらい綺麗なものだった!
なんだコレは! スゴイ! 楽しい! 恐る恐るベットから作品を剥がす。「パリパリッと音を立てながら簡単に剥がれていくサポート部分に驚き、サポートを脱いで出現してきた造形物の滑らかさと硬質感の再現に衝撃を感じた。こうして僕の第二期3Dプリンタトレンドがやってきたのである。
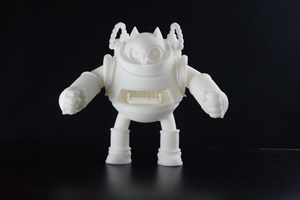
▲AFINIAで出力した習作のキャラメルマン1号セミリアルディフォルメ。(クリックで拡大) |
|
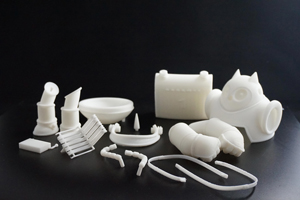
▲細かいパーツから、大雑把に一体化したパーツまで安定して出力できる。
(クリックで拡大) |
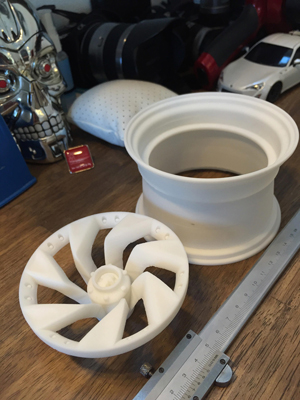
▲バットモービル用にデザインしたオリジナル3ピースホイール。リムの厚みは1ミリでできている。(クリックで拡大) |
|
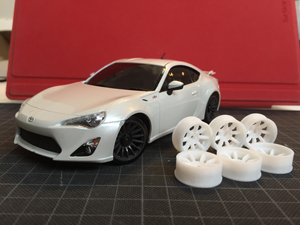
▲ホビー用途としてテスト制作したKYOSHOミニッツ用のホイール。こういったプライベートの楽しみを求めるユーザーも将来は増えていくだろう。
(クリックで拡大) |
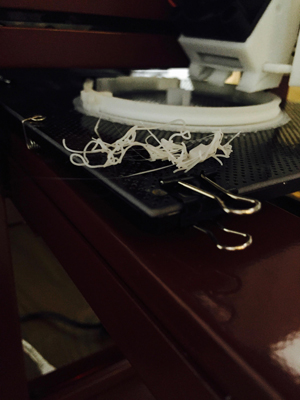
▲出力中のAFINIA。手前のモジャモジャした材料は、プリント初期段階でトーチを温めた際に出てきたものをベットにこすり付けて落としたもの。AFINIAの初期設定に含まれている。(クリックで拡大) |
|
|
・自己満足以外の目的を考えたが
AFINIAが来て以来、とにかくいろいろ試してみた。事業主としては良いといっていいのか、その頃ちょうど1ヵ月くらい余裕があったので、すべてを3Dプリントに集中してみた。ある程度できるようになってくると欲が出てくるもので「もっとキレイにできないか」、「もっと速くできないか」と試行錯誤して数点の作品を仕上げた。
出力された作品を飾ったり、写真を撮ったりと、まるで子供のようだったと思う。ある程度のものができるようになってきた時から考えるようになったことがある。もっと早くに気づいてはいたが出足で目的を失いたくないから考えないようにしていたことだ。
「ソコソコできるようにはなった。後はこれをどうやって仕事に結び付けるか」だ。僕の仕事はサイズ的に大きなものをデザインすることがほとんどで、小さなサイズでは確認には向いていない、その点でコンパクトな3Dプリンタでは無理だろう。それに日常でデザインしたものは大手メーカーさん相手が多く、自社で試作部門を持っているので原寸モデルも作ってしまう。そこにサイズダウンした小さな造形を持ち込んでもインパクトに欠けると思ったからだ。
自分自身「3Dプリントはそもそも仕事のためである必要はないじゃないか」、そう思っていた。最低でもスキルは身に着いたのだし、経験値が上がっただけでもいいじゃないかと思っていた。正直、今もそう思っている。それぐらいの距離感がちょうどよいと思う。
そう考えるとずいぶんと気が楽になるもので、ちょっとチャレンジしたくなってきた。「車の模型は1/10サイズが多い、これを作ってみたい」。まったくもってさっきまで考えていたことと真逆の発想が浮かんできたのだ。「大きいものを作りたい」。そう思ったキッカケは10年前に習作として現代風に自己解釈してデザインした「バットモービル」を出力したいと強く感じていたからだ。「あれが出力できたなら、もうやりきったと言っていいんじゃないか。第一に楽しそうだ」。決意とは案外安直な時にしてしまうものだと今は思う。この決断が自分にとって新しい方向性を見出すことになる。
・3台目の3Dプリンタ「決め手は見た目」
全長45cm 全幅20cmの要素の多いクルマを出力するというのは、そうそう簡単なことではなかった。カーデザイナーが作るキーワークモックアップのような一体造形物であればパーツごとに分割する必要もなく、陶器のような感覚でプリントはできただろう。僕が作りたいと思ったのは、プラモデルのようなスケール模型なのだ。
「自分へのハードルを上げ過ぎた」とも思った。はじめての3Dプリントモデル制作の時のように、地道な厚み作りと組み付けを考慮しながらデータを作りなおすことに目眩もしたが、業務の合間を使って少しずつデータは完成していった。
ある程度の前準備ができた頃、試しにAFINIAで右フェンダー部分を出力してみることにした。そりゃあもう楽しみで仕方がなかった。そしてここで問題が発覚した。何度試しても出力途中で造形が反って変形してしまうのだ。フィラメントがABSなので熱収縮もあるのは分かってはいたが、それまでAFINIAの出力限界サイズを出力したことがなかったので初めての経験だ。
ようするに体積が大きくなれば熱変形も大きくなるというわけだ。熱変形の少ないPLAを試すかとも考えたのだが、この頃は自分でもどうかしていたと思うのだが、「どうせPLAにするなら もっと大きく出したい」と欲が出てきた。
苦労してモデルデータが完成してしまえば後は良いこと尽くめだ、3Dプリンタの機能の限界サイズまで縮小も拡大も簡単にできるからだ。だったら可能な限り大きく出したい。あくまで前段階までの苦労があったからこそ、そういう欲が出てきた。
手持ちのAFINIAは10cm角サイズ程度が出力限界で、長いサイズを出力するには部分的に分割しなければならなく、完成した際におかしな箇所に分割ラインができてしまう。ワンオフモデルとして考えれば組み上げ後にパテ埋めして仕上げればよいのだけれど、ちょっとそれは面倒だし、あまり3Dプリンタの恩恵がない気がしてイヤだった。できれば3Dプリンタで出したまま見栄えが良い方が「アリガタミ」があるように思う。
目的は定まったし3Dデータもほぼ完成に近づいた頃、SNSを通して衝撃的な3Dプリンタを知ることになった。「Atom 2.0」だ。
海外ではすでに発売をしているというAtom2.0はデルタ式で見た目がクールで今まで僕が見たことのないギミックの3Dプリンタだった。そのAtom2.0が日本名「Maestro3D printer」としてクラウドファンディングで出資を集っていたのである。大きなサイズが出力できることが第一条件でもあったし、なによりも見た目がカッコイイということは大きな魅力だ。仮に使わなくなって事務所に置いてあってもオブジェ効果がある。ヨコシマな購入意欲かもしれないが、プラスワンの付加価値は購買意欲を掻き立てるのには重要だと思う。必要だ(欲しい)と思ったら居ても経ってもいられない、考えている時間ももったいない。クラウドファンディングなど一度もしたことがなく少々の不安も感じながら、1台分の先行購入の投資を決めたのである。
以下次回。
次回は2月中旬に水野氏の後半を掲載します。
(2018年1月29日更新)
|