●吉田氏の3Dプリンタ遍歴
2014年~「Form1」購入価格:当時本体40万円程度で消耗品込み約50万円で輸入
2015年~「Form1+にアップグレード」「SCOOVO X9」購入価格:当時25万円程度
2016年~現在「UP BOX」購入価格:40万円程度
・3Dデザインツール
Rhinoceros、Grasshopper、Fusion360など
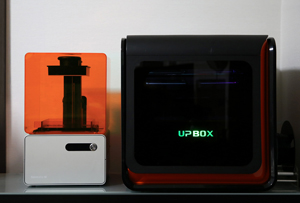
▲吉田氏の選んだ3Dプリンタ。左が「Form1」、右が「UP BOX」。筐体の色がたまたまオレンジに揃った。(クリックで拡大)
|
|
|
・はじめに
はじめまして。「SHINYA YOSHIDA DESIGN」という名前で活動しております吉田と申します。僕は主に生活用品などのプロダクトデザインを中心に、さまざまな分野の製品開発を部分や全体でサポートするような業務をしております。普段から3Dプリンタを含むデジタルファブリケーションツールの使用や、プログラマーと協業したデザインツールの開発など、さまざまな場面でデジタルツールを使用することも多いです。
ここ数年3Dプリンタメーカーが乱立し、正直どのモデルを選んだら良いのか分からなかったりするかと思います。今回は3Dプリンタに関する経験の簡単な紹介となりますが、今後3Dプリンタを導入される上で何かご参考になれば幸いです。
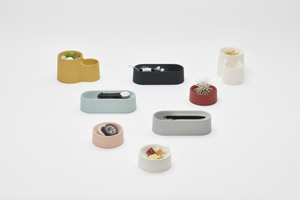
▲3Dプリント型によるバキューミングで試作開発され2017年ミラノサローネサテリテで発表された「トレー」。(クリックで拡大)
|
|
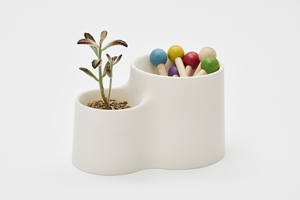
▲同トレー。2018年6月よりニューヨークのブランドから発売開始されます。
(クリックで拡大) |
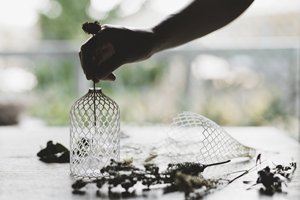
▲「3D Printed Flower Vase tint」。3Dプリンタで製造され手仕事で着色された花器。(クリックで拡大) |
|
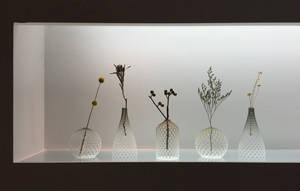
▲ショップに並ぶtint。(クリックで拡大)
|
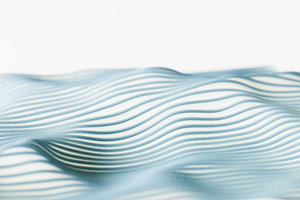
▲Grasshopperなどのシミュレータで自然界にみられる“ゆらぎ“を再現し3Dプリントしたトレー。表と裏でカラーが異なり、海と山に見える。(クリックで拡大) |
|
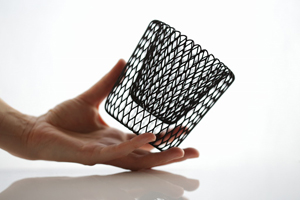
▲チタン3Dプリントによる「キャンドルホルダー」。
(クリックで拡大) |
・3Dプリンタとの出会い
3Dプリンタとの出会いは学生時代まで遡ります。3Dプリンタの存在自体はかなり前から知っていましたが、実際に自分の作品として利用したのは今からちょうど10年前になる2008年頃でした。その時はデザインコンペの二次審査用の試作で、機種は正確に把握していませんでしたが液体レジンをレーザーで硬化させるものだったと思います。
当時学生でしたのでかなり安くしていただき、数万円で手のひらサイズの出力品を数個作ってもらいました。しかし結果は自分でマスターを作って注型した物の方がよっぽど綺麗でがっかりしたのを覚えています。当時は機械の特性や積層痕の処理、後加工性などはよく考えていなかった故の失敗でした。
・3Dプリンタ「Form1」の導入
SLA方式/造形サイズ:幅125×奥行125×高さ165/最小造形ピッチ:0.025
https://formlabs.com/ja/
事業化してからはじめて導入した3DプリンタはMIT出身者らが立ち上げたFormlab社の「Form1」でした。オレンジ色の透明アクリルとマットなアルミ筐体の組み合わせはとても印象的で、当時とても物欲を刺激されたのを覚えています。この機種はSLAと言われる方式で、透明タンク内の液体レジンをレーザーで硬化させて吊り下げ型のプラットフォームに造形するタイプです。Form1は発売前からクラウドファンドでもかなり話題となっており、日本への配送サポートがない頃の初期ロットをアメリカから直接個人輸入しました。
プリンタを操作する「Preform」と言うアプリもとても優れており、ベース厚みやサポートの生成角度と密度を3Dプレビューで見ながら視覚的にコントロールでき、他にはない直感的な使い心地にとても可能性を感じていました。
レーザー系の機種は、FDM方式のモーター音とは違い、やや静音で夜間の造形は快適です(レジンタンクの昇降音はします)。造形精度は細かい造形物も3次元的な歪みはあるもののデザインを確認するには十分で、優秀なアプリのおかげもあり、かなり満足していました。当時の不満な点としては、IPA(イソプロピルアルコール)による洗浄の手間、レジンのランニングコスト、タンク寿命などでした。
まず洗浄に関しては、アルコールによる洗浄が思っていたより大変でした。造形後プラットフォームからべりっと剥がしたらすぐに使用できるFDMとは違い、アルコールに10分ほど漬けて硬化していない表面のレジンを落とす必要があり、洗浄後もまだ表面はベタベタするので紫外線ランプか太陽光でしばらく硬化と乾燥をする必要がありました。
この機種の紹介動画ではPCのすぐ脇で操作するイメージがありますが、可燃性のアルコールを使うため、ゴム手袋、ウエス、トレーなどと換気のできる広めの作業環境の確保は必須と言えます(可能であればエアガンとコンプレッサーがあると乾燥が楽です)。
後継機種のForm1+とForm2からは飛躍的にレーザー出力が上がりレジンの硬化不良は大幅に改善しているので造形後の洗浄はかなり楽になっています。
次にレジンコストですが、1リットル(約1キロ)のレジンでアメリカからの輸送費を入れると15,000円~18,000円くらい掛かっていたかと思います。一般的なFDM用のABSフィラメントで言えばキロ3,000円からで純正でも5,000円程度なので、造形失敗時のダメージは結構大きかったです。
またこの方式の弱点として、レジンタンク底の透明シリコン層の汚れと傷で到達するレーザーが弱まり造形不良を起こし、シリコン層に付着してまた傷が増えるといった悪循環が起こるため、タンクは消耗品でした(タンクの価格は輸入費用込みで1万円弱だったと思います)。
タンク底のシリコンを汎用シリコンで張り替える方法を、あるユーザーが公開しており僕も試しましたが費用と手間を考えるとタンクのまとめ買いのほうが安いと感じていました。後に不具合が多くなりFormlabに報告すると運よく中身だけを無償でForm1+と交換することができ、レーザー出力が上がったことで一時的に解決しましたが、現在は清浄時間などをあまり割けないため殆ど動かしていない状態です。
Form1とForm1+の総評としてはサポート位置や太さなどを視覚的にコントロールできるアプリとデザイナーの用途では十分な精度と造形スピードは非常にコストパフォーマンスが高いと思います。最新のForm2ではレジンの自動補給や保温、タンクのワイパーなどForm1での不具合の改良点がいくつもあるのと、洗浄と硬化促進キットのオプションなども用意されているので、現時点でもお勧めできる機種の1つです。
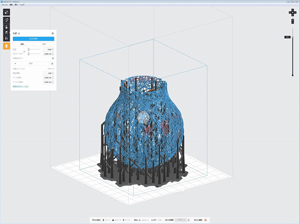
▲Form1Preformによるサポート生成のカスタマイズ画面。(クリックで拡大) |
|
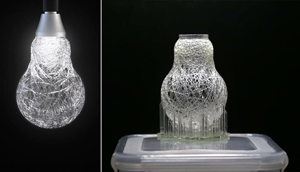
▲左レンダリングと右Form1による出力品。
(クリックで拡大) |
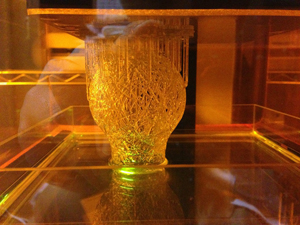
▲出力中の様子 造形物下部の緑の発光がレーザー光。(クリックで拡大) |
|
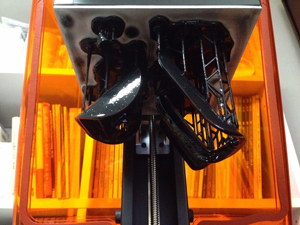
▲出力後のプラットフォームの様子。(クリックで拡大)
|
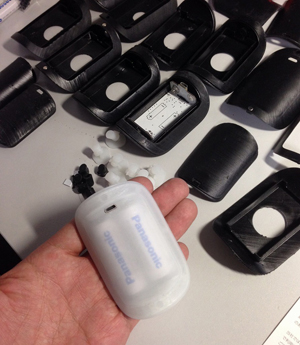
▲出力品による試作検証 0.05mm単位で勘合と外観をチェックしている時の様子。(クリックで拡大) |
|
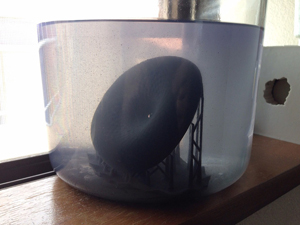
▲IPAによる洗浄中の様子 10分ほど漬けた後にウエス等で洗浄する。
(クリックで拡大) |
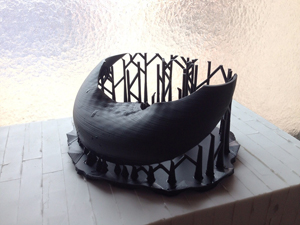
▲造形途中で失敗した出力品
。(クリックで拡大) |
|
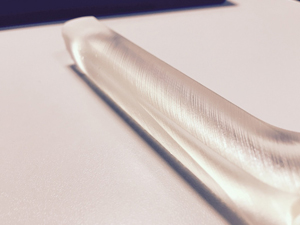
▲Form1透明レジンの美しい積層痕。(クリックで拡大)
|
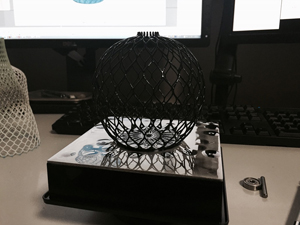
▲Form1出力参考品 tintの繊細な構造も印刷が可能。(クリックで拡大) |
|
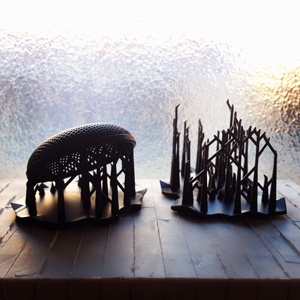
▲出力品に劣らず美しいForm1のサポート。(クリックで拡大)
|
・2台目「SCOOVO X9」の導入
FDM方式/造形サイズ:幅200×奥行170×高さ230/最小造形ピッチ:0.05
http://abee.co.jp/3dp/scoovo/x9/
Form1の造形不良が増えてきた時期に保険的に購入したのは、純国産プリンタを謳った「SCOOVO X9」という3Dプリンタでした。FDM方式のプリンタすべてに言えますが、電車のドレミファインバーターのようなモーター音が夜間は結構気になる音量なのと、樹脂の匂いもあり、設置場所には考慮が必要です。
この機種はプラットフォームがオープン型なのもあり、作動音軽減とフィラメントの湿気対策や温度管理も含めて段ボールやアクリル製の囲いを追加した方がよい機種でした。最小ピッチは0.05mmとFDMの中では高精細ですが、造形速度とアプリの操作性はForm1に比べてやや劣り、僕の業務用途で求める「少々粗くてもいち早くフィジカルチェックするための道具」としてはやや不満な点もありました。
専用アプリSCOOVO STUDIOでは簡単モードとアドバンスドモードの2つのモードが用意されており、アドバンスドモードでのGコードの編集による細かなカスタマイズを行えば、かなり高精度な出力が可能です。この機種のプラットフォームはガラス製で、ポリイミドテープというフィルム状の耐熱テープで造形物を定着させます。このポリイミドテープは幅広のものを使うのがお勧めで、テープ表面がとても平滑なので造形物の底面は射出成型品のようにきれいに仕上がるメリットがありました。
総評としては、時間をかけたトライ&エラーが必要になるので、人員の少ない事務所では少々オペレーションが大変なところもあるかなと思います。時間をかけてセッティングを追い込めばかなりの高精度で造形ができるので、その辺りのバランスを考慮した導入検討が必要です。
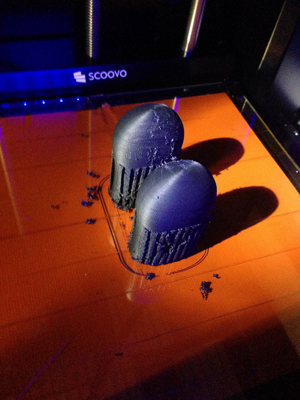
▲SCOOVO X9出力品 積層ピッチ0.1mmで滑らかな仕上がりで印刷が可能。オレンジ色のプラットフォームに見える分割線がポリイミドテープの分割ライン。(クリックで拡大) |
|
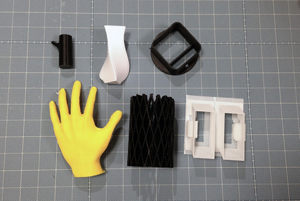
▲SCOOVO X9による出力品。(クリックで拡大)
|
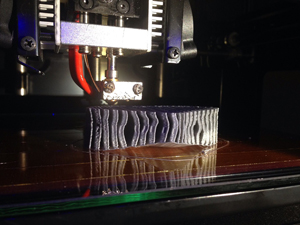
▲SCOOVO X9の造形失敗例。プラットフォームへの定着失敗(ABS)。(クリックで拡大) |
|
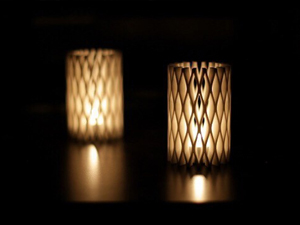
▲ABS白の出力品をLEDキャンドルで発光させたもの。(クリックで拡大)
|
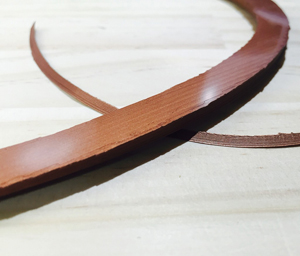
▲銅フィラメントテストの様子 ポリイミドテープ(プラットフォーム)側はつるつるの表面になる。(クリックで拡大) |
|
|
・3台目「UP BOX」の導入(現在のメイン機種)
FDM方式/造形サイズ:幅255×奥行205×高さ205/最小造形ピッチ:0.1
https://www.tiertime.com/
Form1とSCOOVO X9を用途に応じて使い分けておりましたが、徐々に大きな造形物とスピードを必要とされる場面も増えたのを機に「UP BOX」を導入しました。
UP/AFINIAの後継機種で造形エリアがW255×D205×H205ととても大きく重宝しています。3Dデータを積層データに変化するスライサーも優秀で、サポートの切り離し易さ、造形精度、安定感は従来機と同様に高く、故障もFDMお決まりのノズルのつまり程度なのでメンテナンスやトラブル対応も比較的楽な方だと思います。
従来のモデルと異なるのは、本体が樹脂のボディで覆われることで作動音と匂いの軽減、ノズル温度の安定性などを大幅に向上している点です。どの方式でも長時間のプリントや連続した使用が続けばトラブルも増えるので、僕の事務所ではエクストルーダーと言われる射出ユニットは3台体制でノズル詰まりが起きたらメンテナンス済みのものと交換することで最小限の時間でトラブル対応する工夫をしています。
不満な点を挙げるとすればUP STUDIOという専用アプリはサポートのセッティングにプレビュー機能がないので少々分かりづらく操作しづらかったことですが、日々のソフトウェアアップデートで徐々に良くなってきています。
この機種に限らず、今までにあらゆるメーカーのフィラメントを試しましたが、メーカーと樹脂の種類によってはサポートの剥がれが悪くなったり、造形失敗率が上がったりという現象が起こるので、現在は純正品のABS黒しか使わなくなってきています。現状、外観を問わない目的での利用がほとんどになっているので樹脂を限定することで失敗率を下げるようにしています。
FDM方式の特性上、湿度や温度などの環境にプリント品質が左右されることも多く、汎用の樹脂ケースとシリカゲルを用いたフィラメントの湿気対策や温度の安定化のためにBOXを併用される方も多いかと思いますが、僕の場合は樹脂の消費スピードが速いので、ほとんど対策していなくても特に問題は出ていません。UPシリーズもそうですが、最近のFDMはオーバーハング形状にも強く、多軸のプラットフォームによるサポートレス印刷技術なども研究が進んでいるので今後のFDMの進化には期待しています。
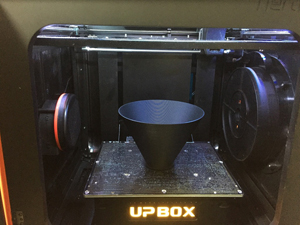
▲3Dプリント塗装冶具を印刷したもの。左側の突起はフィルターとなっておりABS粉塵と匂いを軽減していると思われる。(クリックで拡大) |
|
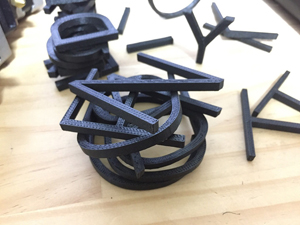
▲展示会の壁面サインを3Dプリントしたもの。何度でも再利用可能な樹脂製の立体サインが作製可能。(クリックで拡大)
|
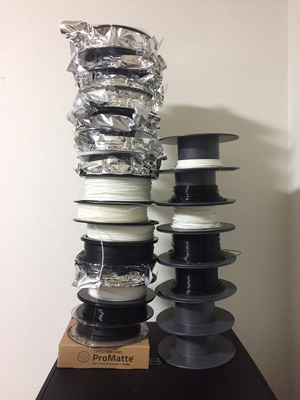
▲さまざまなメーカーのテスト中。大量消費されるフィラメントたち。(クリックで拡大) |
|
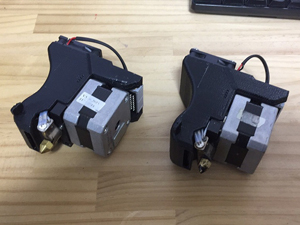
▲UP BOXの予備のエクストルーダーユニット。(クリックで拡大)
|
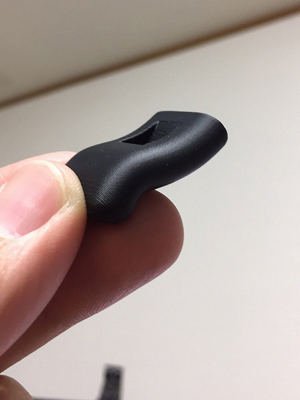
▲0.2ミリのピッチでも十分になめらか。(クリックで拡大) |
|
|
・仕事での3Dプリントの役割
仕事の内容によっても異なりますが、僕の場合は強度を満たす稼働部や嵌合部などの部品設計も多く、限られた設計時間の中での作動確認には手元に3Dプリンタがあることは必須になってきています。
現状の3Dプリントの目的を大きく分けると、設計の確認のためのプリント、プレゼンやコミュニケーション用のプリント、実際に使用する部品のプリント、冶具や型のプリントの4つに分かれます。
最近の事例の1つではFusion360の解析機能を使用した耐荷重部品の設計を行い、事務所の3Dプリンタでサイズや機能を確認、その後、SLS3Dプリント品による破壊試験を繰り返し行うことで、耐荷重が数トンにもなる射出成形の部品を設計したということもありました。
その他には2017年ミラノサローネサテリテで展示した樹脂製のトレーの試作にてABSでプリントした型を使用したバキュームフォーミングを行いました。始めはABS型が熱と大気圧に耐えられなくて失敗しましたが、徐々に条件を出していき、シェル厚み、インフィル密度、冷却時間、ブローとバキュームタイミングなどの組み合わせを調整することで、形状の深い成形難易度の高い形状もきれいに成形することができました。
3Dプリント品を冶具やマスター型にした素材の置き換えは、モックアップ屋さんでは昔から行われていたことだと思いますが、デザイナー自らが手元の3Dプリンタと他の加工を複合的に使いこなし、デザインの確認や模型作りを高精度で行えるメリットは非常に高いと実感しています。
そして今後3Dプリンタに望む技術としては、デザイナーの負荷となる3Dプリントのためだけの厚みデータ作りの効率化です。実際の製造方法とは異なるため専用のデータとなり3Dプリント以外には役に立たないので、その非効率な部分を3Dプリンタ側のアプリケーションが担い、サーフェスモデルを各プリンタの特性に応じたデータへと変換し、最適な3Dプリントで再現してくれるといいのに、と感じています。
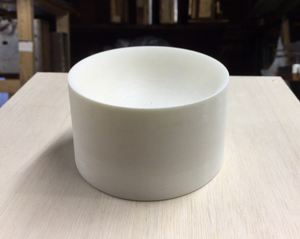
▲ABS 3Dプリント型。(クリックで拡大) |
|
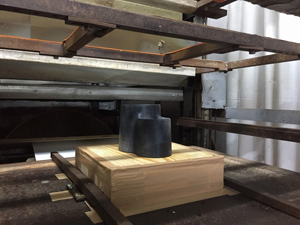
▲ABS 3Dプリント型がバキュームフォーミングの機械にセットされた様子。
(クリックで拡大) |
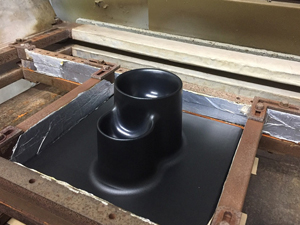
▲バキュームフォーミング後の様子。(クリックで拡大) |
|
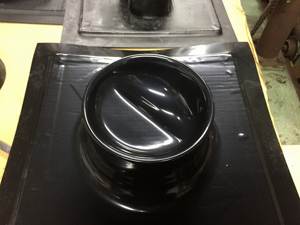
▲使用材料によって色、ツヤ、シボなどの素材と表面テクスチャの選択が可能。
(クリックで拡大) |
・3Dプリント製品と実用品の実験
3Dプリンタは試作や検証の道具として、またお客さんやエンジニアとのコミュニケーションツールの1つとして捉えていましたが、adidasのFuturecraft 4DやMITのRapid Liquid Printingなど新たな3Dプリント技術で製造された最終製品を手にする時代がすでに来ているので、自分自身でも実験をしながら活用していこうと考えています。先述の3Dプリントと親和性の高いバキュームフォーミングもそうですが、出力品の塗装や後処理までを含めた提案は今後CMFデザインの1つの要素となってくると思うのでとても興味があります。
過去の実験的試みの1つは冒頭の紹介画像にもありました3Dプリント製のフラワーベース「tint」です。tintはナイロンSLSで3Dプリントされた後、3Dプリント冶具を使用してグラデーション状の塗装を行っています。このフラワーベースはあくまでも3Dプリントであることを主体とするのではなくテクノロジーに関係なく女性が欲しいと思えるような質感やCMFの製品を目指したのがきっかけでした。日本では2015年からSEMPRE HOME、東急プラザ銀座、海外ではイタリアのRinascenteで販売していただいています。
また他の事例では、昨年大阪で開催された「COMPOSITION 2017」というプロダクトデザイナーが「3Dプリントジョイントを使ったDIYを提案する」というテーマの展示に参加させていただき、実用に耐える3Dプリントジョイントを使ったローテーブルを発表しました。このテーブルはジョイントにボルトを締め込むことでジョイントとステンレスパイプ内壁に発生する面圧で強固な構造体を組み上げるといったものです。
今後はますます金属やガラスなどといった素材などの3Dプリント技術も実用化が進んでいくと思うのでとても楽しみにしております。
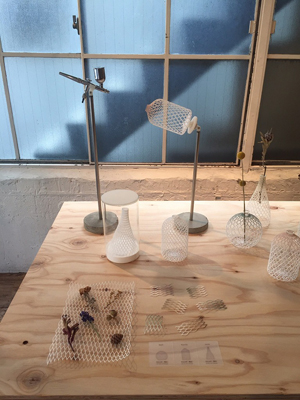
▲フラワーベースtintと3Dプリントされた塗装冶具と展示什器。(クリックで拡大) |
|
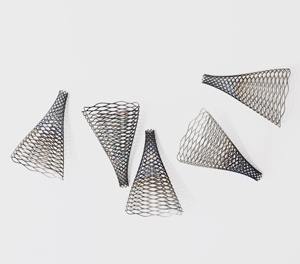
▲チタン3Dプリント製のtint。
(クリックで拡大) |
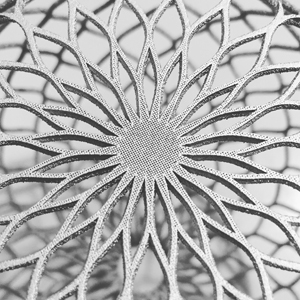
▲tintのアルミ3Dプリントのテスト。(クリックで拡大) |
|
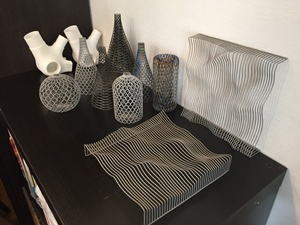
▲グレー色すべて金属3Dプリント出力品。
(クリックで拡大) |
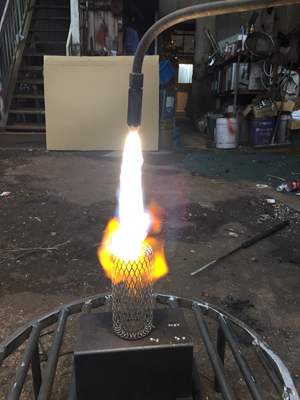
▲ステンレス3Dプリント品の焼き入れ。(クリックで拡大) |
|
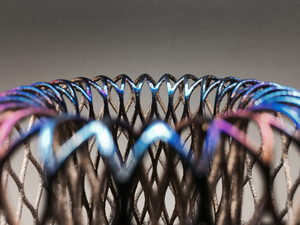
▲焼き色のついたステンレス3Dプリント品。
(クリックで拡大) |
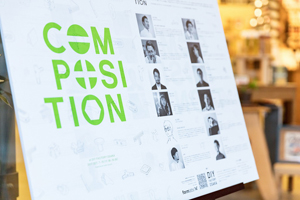
▲COMPOSITION2017の様子1。(クリックで拡大) |
|
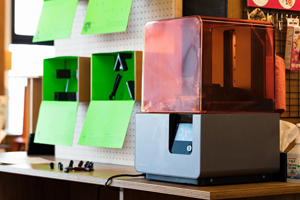
▲COMPOSITION2017の様子2。
(クリックで拡大) |
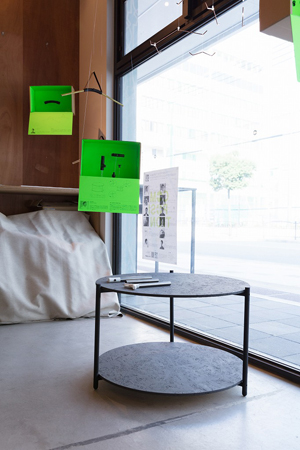
▲COMPOSITION2017の様子3。(クリックで拡大) |
|
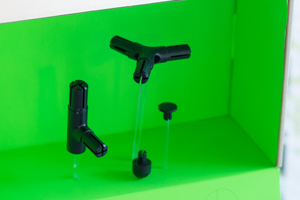
▲3Dプリントされたジョイント。
(クリックで拡大) |
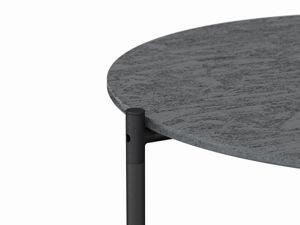
▲COMPOSITION2017で発表したローテーブル。(クリックで拡大) |
|
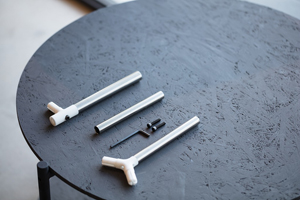
▲3Dプリントされたジョイント。
(クリックで拡大) |
次回は川本尚毅さん(プロダクトデザイナー、エンジニア)です。4月中旬掲載。
(2018年3月26日更新)
|