●向山氏の使用3Dプリンタ
2013年 Prusa Mendel(改)1台
2015年 Prusa i3 2台
・3Dデザインツール
Rhinoceros、Grasshopper、Fusion 360など
・はじめに
STUDIO REVENTの向山と申します。STUDIOといっても自宅で3D系のツールと3Dプリンタを使用して小規模で作業をしております。元々は造形関連の試作、コンポジット関連のハードモデラーの現場職だったのですが、時代の流れもあり、ある程度データ関連業務も兼務していくようになりました。
3Dプリンタ自体は趣味として始めた感じですが、現在では主に3Dプリントと伝統工芸の木目込み人形などに用いられている工法(木目込み:あらかじめ本体に彫られたミゾ、筋彫りに貼りこんだ布の端末を押し込む)を組み合わせた作品の制作をメインに3Dプリンタを使用しております。
・まずは試しに3Dプリンタを購入
当初は木目込み用のボディを制作するのにミニCNCの購入を考えていましたが、自宅で作業するのに
(1)切削の際に粉が出る
(2)オーバーハングのある場合、分割や両面切削が面倒
(3)ビルドエリアのサイズの小ささ
などに難点があり、3Dプリンタの購入を考えていました。
3Dプリンタという呼ばれ方をする以前から、以前の業務で光造形や粉末焼結積層は知っていたのですが、個人で比較的低価格で購入できそうな3Dプリンタは、初代のMakerbot社の「Replecator」しか知りませんでした(当時は「Cupcake CNC」という商品名だったと思います)。
当時は動画などででき上がった出力物を見ると、購入しようと思える品質ではなかったのですが、徐々に品質や価格面で選べる3Dプリンタが登場してきたため、日本語でのサポートも受けられる「Prusa Mendel(改)」を試しに購入することにしました。本当は「UP! Plus」が欲しかったのですが、ビルドエリアが若干狭いために、断念しました。
まだこの頃は現在のように、10万円以下の製品では、プリンタ全体を筐体で覆うようなタイプはほとんどなかったように思います。それを考えると近年の低価格3Dプリンタはかなり充実しているなあと感じます。
・苦戦しながらいろいろなものを出力、本体を改良、そして2、3台目を購入
もちろん最初は小さなテストピースの作成から始めたのですが、当時制作したかったものはサイズが大きかったため、実際に出力しだすとヒートベッドからのはがれや、ホットエンドの変形でフィラメントのロードが上手くいかないなど、かなり苦戦しました。
当時は今ほど3Dプリンタの出力のコツなどの情報が少なく、ホットエンドの変形などは無理やりポリエステル樹脂とカーボンで補強して使用していました。
また木目込み用のボディ以外にも、CFRP(Carbon Fiber Reinforced Plastics:炭素繊維強化プラスチック)用のパネル反転用ツールやバキュームフォーム用の型なども制作したりと出力に苦戦しながらいろいろ試していきました。
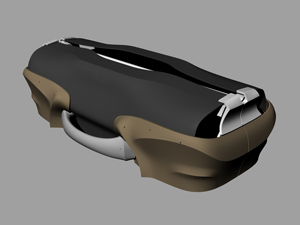
▲ドローン用折り畳み収納ケースのデータ。(クリックで拡大) |
|
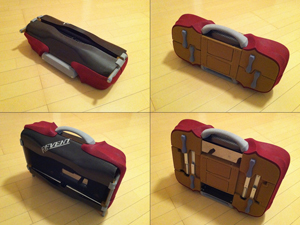
▲本体は3Dプリント後に生地を貼り、木目込み仕上げ。(クリックで拡大)
|
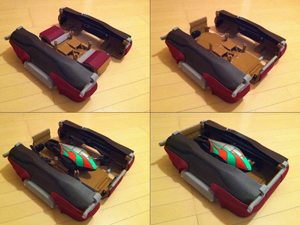
▲黒いパーツは反転用ツールを3Dプリント後にCFRPに反転。(クリックで拡大) |
|
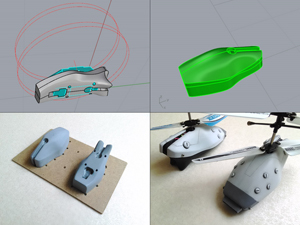
▲ラジコンヘリのボディのバキュームフォーム型を3Dプリント。(クリックで拡大)
|
正直なところ一番最初に選択した機種としては個人的には失敗したなあという感じで、何故かヒートベッドをONにすると積層痕の乱れが激しく、特にABSで出力するとキレイに出力できる状態ではありませんでした。
この問題を解決するために、ヒートベッドの別電源化やZ軸をリードスクリューに変えるなど改良しましたが、限界もあり2、3台目の「Prusa i3」を購入しました。
2、3台目は前回の失敗があるので、まずは1台を購入して様子見をしたのちに3台目を購入しました。
製品自体は中国製でサポートも日本語はなく、基盤のヒートシンクやエンドストップスイッチの配線が一部取れていたりなどのトラブルもありました。
3台目を購入の際はアクリルフレームが割れてしまっていたためフレームのみ配送してもらうなどありましたが、対応も良く、組み立ても動画で分かりやすかったのを覚えています。中国製に限らず3Dプリンタは完成品、組み立て式も含めていろいろあるため、とにかく購入してみないと分からないと感じました。
この頃は低価格3Dプリンタでもホットエンド下を冷却するファン、ダクトが付属するようになっていましたが、ダクトのレイアウト、冷却風の巻き返しなどでノズル温度が安定しないなどの問題点がありましたが、多少の改良で改善しました。
また3Dプリンタの買い替えを機に3Dプリンタ周辺の雰囲気温度の安定化や静音、匂いの排気の改善をするために専用ボックスを作成しました。専用ボックスまで作成するとさすがに最初から筐体で覆われている3Dプリンタを購入すれば? と自分でも思ったのを覚えています(笑)。
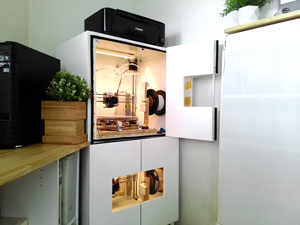
▲2、3台目を機に作成した専用ボックス。(クリックで拡大)
|
|
|
・3Dプリントサービスを使い分け
業務でも作品の制作においても所有している3DプリンタはFDM(熱溶解積層)のシングルヘッドのため、出力後のサポート外しなども考慮するとどうしてもうまく出力できない場合があります。
3Dプリント出力サービスはデータをアップロードするとすぐに出力可能な材料から価格までわかるサービスが多いため、形状によっては3Dプリント出力サービスを活用することもあります。
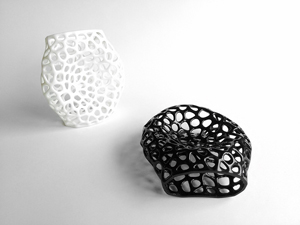
▲所有の3Dプリンタで出力(出力後にアセトンべーパー処理)。(クリックで拡大) |
|
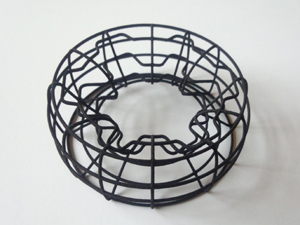
▲形状によっては3Dプリント出力サービスを活用。(クリックで拡大)
|
・出力特性を生かした木目込みボディ制作
最後にもっとも活用している3Dプリントによる木目込みボディ出力の紹介になります。
元々は「最小限のパーツ点数で、多材質感を表現できる面白さ」から趣味として木目込みを取り入れていろいろなものを作っていました。今までは作っていく過程で3Dデータを作成しても、断面図くらいしか使えないため、データをそのまま活かせる3Dプリンタは非常に魅力的でした。特にFDM方式の3Dプリンタは木目込みボディの出力に対して相性が良く、
(1)マテリアルを貼り込むため積層痕が気にならない
(2)結果として積層ピッチが荒くでき、比較的短時間での出力が可能
(3)注型と違い、脱型後の離型剤の除去などを必要としないなどのメリットがあります。
難点としてスライサーでのサポート設定がしにくいなどがあります。出力物に対してマテリアル貼り込み後の端末処理は、本体に彫られたミゾ(木目込みミゾ)に押し込むのですが、木目込みミゾは幅数ミリ、深さ3から5ミリ程度のため、シングルヘッドでサポート設定ありの状態で出力するとサポート除去が困難になりがちです。
そのため木目込みミゾのモデリングは基本的にはサポート設定なしで3Dプリンタのメリットである、ある程度のオーバーハング出力ができる点を最大限生かすようにしています。
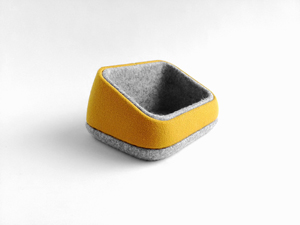
▲小物入れ(出力は2ピースで全体を木目込み仕上げ)。(クリックで拡大) |
|
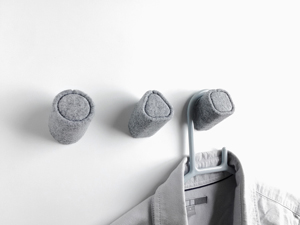
▲○△□フック(各本体は1ピースで全体を木目込み仕上げ)。(クリックで拡大)
|
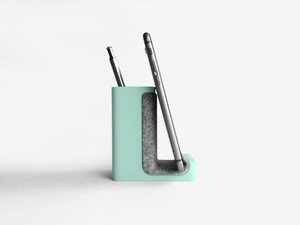
▲スマホも置けるペンスタンド(部分的にフェルトを貼り木目込み仕上げ)。(クリックで拡大) |
|
|
また最近では出力物を部分的な貼り込みにすることでフィラメントのカラーを生かしたりなどの試みもしています。
3Dプリンタはデータを作成して簡単に形にできる面白さもありますが、さらにひと手間加えることでいろいろな楽しみ方があるのではと思っています。
次回は東方秀樹さんです。9月下旬掲載予定。
(2018年8月13日更新)
|