●松本氏の主な使用3Dプリンタ
2018年「Anycubic i3 mega」購入価格 36,000円
2019年「自作3Dプリンタ vol.1」制作費 約90,000円
2019年「自作3Dプリンタ vol.2」 制作費 約24,000円
・3Dデザインツール
Fusion 360 など
・はじめに
はじめまして、中小企業内で3Dモノ作りを推進している、松本 学と申します。私の職場への3Dプリンタの導入を行うにあたって、その経緯や、なぜ3Dプリンタの自作を行うのかなどのお話をさせていただきながら、生産技術者目線の3Dプリンタの有用性・魅力をお伝えすることができればと思います。
・3Dプリンタとの出会い
2015年のある日、「3Dプリンタセミナー」と書かれたチラシをふと目にし、会場のシェアオフィスも職場に近かったため興味本位で申し込みました。セミナー当日、受講者は私ともう1人のみで、2台設置されていた「MakerBot Replicator 2」を各自で操作しながらボルトとナットの造形出力を行い、それを手にした私は、あらゆる工程をすっとばして、ものの10分程度で突然機械部品を手にしたことについて衝撃を受けたことをよく覚えています。
・3Dプリンタを活用した生産設備改善
はじめて3Dプリンタに出会ってから数ヶ月後、社内である工程の自動化に関わる仕事に取り掛かり、自動機の組立て、設置、試運転、現場納入から量産稼働まで行いました。そこで自動機内で手のひらサイズの製品を高速で搬送するユニットにおいて、製品のぐらつきによる脱落が発生するという不具合に直面しました。
ぐらつきを抑えることができる冶具を作るにあたり、当時フリーソフトの3D CAD「123D Design」とシェアオフィスの3Dプリンタを活用することで、非常に安価でしかもスピーディーに不具合を解消し、自動機チョコ停解消と保全工数削減による大幅な生産性向上、そしてコスト削減を達成することができました。
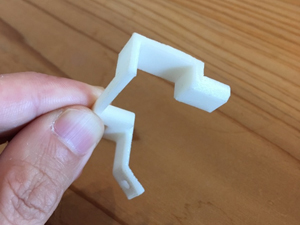
▲3Dプリンタで造形した治具。40分程度で造形可能。(クリックで拡大) |
|
|
しかしここで3Dプリンタ造形の難しさにも直面しました。狭い自動機の中に設置した3Dプリント冶具が少しずつ製品と干渉し、その際に製品から受ける力によって、積層面沿いにポキッと折れてしまいました。その時初めて積層方向が造形品の耐久性に影響することを知った私は、造形をお願いしていた3Dプリンタ技術者と相談し、3Dプリンタの積層方向を工夫してもらいつつ、冶具形状を補強することでなんとか冶具の耐久性を向上させることができました。
・「工具」としての3Dプリンタとそれを使う「職工」とは
それからも趣味の範囲で、モノ作りの部品作成にシェアオフィスの3Dプリンタを使用していましたが、造形途中に異常停止してしまうこともしばしば起こり、どこか工具としては頼りなさを感じていました。そもそも3Dプリンタの構造や制御回路、ソフトウェアを私自身理解することができていないことがその原因であると思いました。
上記の生産設備改善後も、「突然冶具を出力するミステリアスな箱」である3Dプリンタへの社内の興味は深まることはありませんでした。そんな中、突然新規事業獲得のために3Dモノ作りの仕事が発生。これから1人の職工として3Dプリンタを職場へ導入し、仕事へ応用していく中で、「造形品を受け取る方」へ安心していただける人間とは何者かを考えるようになりました。
・3Dプリンタを作ろう
生産設備の保全、改善業務を行っていた中で、私の目の前で設備を使用する現場の方々にもっとも安心を与えたのは、その設備を知り尽くした作り手でした。それならば社内で3Dプリンタを設計し、組立て、造形する人間に私がなってしまおうと考え行動をはじめました。
調べてみるともっとも汎用性の高いFDM(熱溶解積層法)タイプの3Dプリンタを安価に自作している方は世の中に多く、Reprapという方式のオープンソース3Dプリンタの作成事例などの情報も豊富に存在していました。部品もすべてAmazonですぐに手に入る。あとは背中を押してもらえる人と組立ての環境を探すだけでした。以前からお世話になっていた3Dプリンタ技術者に相談し、職場からそう遠くないファブラボでの工作をはじめました。
自作3Dプリンタがある程度形になった段階で、細かい部品をファブラボの3Dプリンタで造形していましたが、この時点で、どうせなら自宅にも1台3Dプリンタを置いて好きに使ってしまおうと思い、Anycubic i3 MEGAを購入しました。しかしここでも3Dプリンタ造形の難しさに直面しました。造形品が途中でテーブルからはがれ、うまく造形することができない。ここでも先輩技術者へ相談し、テーブルのレベリング方法や、ヒーテッドベッドとホットエンドの適切な温度設定方法、スティックのりを使用したテーブルの定着力改善方法についてアドバイスをもらい、徐々に安定して造形を行えるようになりました。
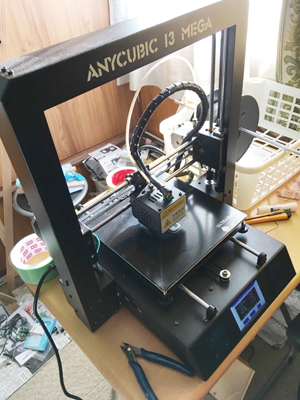
▲Anycubic i3 megaを自宅用に購入。(クリックで拡大) |
|
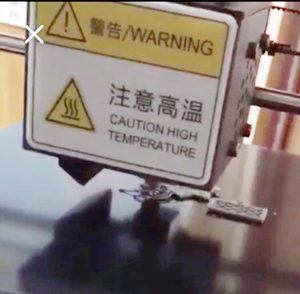
▲造形中にテーブルから造形品がはがれてしまっている。(クリックで拡大)
|
・自作3Dプリンタが完成し、職場へ導入
こうして半年ほどで自作3Dプリンタの組立てが終了し、職場への導入をはじめたときに2つの問題に直面しました。1つ目はZ軸方向に動く機構が組立て後の調整不足によりリードスクリューという部品と■?み込んでしまい、かなりの異音とともに振動し始めたため非常停止させました。もう一度組付け精度を確認するため、デジタル水準器を使用してXYZ各軸の機構の水平垂直精度が確保されているかを細かく見直しました。
2つ目は造形品の造形品質不良、特に「ウーズ」と呼ばれる現象と積層痕が目立つ問題が発生しました。ネットで情報を集め、スライサーのパラメータの設定値を改善することで造形条件のキャリブレーションを実施し造形品質を向上させ安定出力できるようになりました。この時点での満足度は80点で、概ね合格点に到達できたかなという印象です。
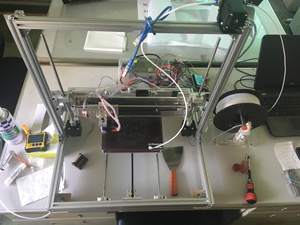
▲自作3Dプリンタvol.1の外観。(クリックで拡大) |
|
|
こうなるとどんどん楽しくなってきます。小さいものからある程度ボリュームのあるものへ造形チャレンジしたり、構造が複雑なものの造形を行ったり、実際の製品を造形して寸法誤差を検証してみたりしながら、さまざまな造形品を職場で展示し社内の技術者に見てもらいました。次第に良い評価を受けるようになり、ついに社内でも産業用の3Dプリンタ導入の動きが開始されています。
・3Dプリンタをみんなのものに
3Dプリンタを取り巻く状況はここ1年ほどで激変してきています。非常に高強度な造形品を高い造形品質で出力できる3Dプリンタが、数年前では考えられないほど安価に販売されていたり、私の職場の周りでも大中小の機関が最新の産業用3Dプリンタを購入し精力的にセミナーを開催しています。
こうした流れの中で、3Dプリンタを活用したモノ作りをもっと手軽に、身近に感じてもらえないかと考え、造形範囲がX100×Y100×Z110mmのポータブルな3Dプリンタを自作してみました。多くの部品は自作の3Dプリンタ vol.1で造形し、簡単に組み立てられるようにしてあります。
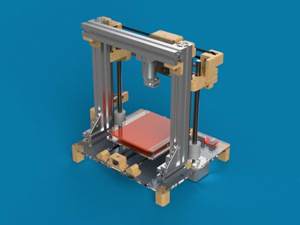
▲自作3DプリンタVol.2。(クリックで拡大) |
|
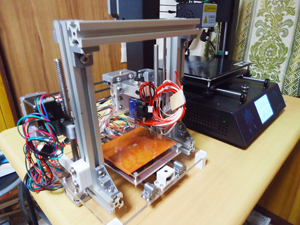
▲自作3DプリンタVol.2をセットアップ。(クリックで拡大)
|
この自作3Dプリンタvol.2を片手に、さまざまな方々とお会いし、モノ作りのアイデアを生み出しながら、3Dプリンタをみんなのものにできたらと思い、日々活動してまいります。
次回は大谷和利さんです。2019年4月下旬掲載予定。
(2019年3月11日更新)
|