●光造形方式3Dプリンタの「SparkMaker」でバッジを作る
前回のコラムの最後に、「次回は、再び100円ショップのアイテムと3Dプリンタパーツを組み合わせて、Telloでのレース用のコースマーカー的なものを作った顛末を紹介する予定だ」と書いた。これまでの回で使ってきたのと同じFDM方式の3Dプリンタによる作例として紹介するつもりだったが、本連載が都合により今回で休載となるため、急遽、先ごろ入手した光造形方式の3Dプリンタである「SparkMaker」で製作した作品の紹介に切り替えてお届けすることとし、両者を比較した感想を述べて、コラムの締めくくりとしたい。
今回紹介するのは、今年で設立50周年を迎えた大阪女学院短期大学の記念式典において主に学生ボランティアの皆さんに身につけていただくために無償で作ったものである。
家庭用の3Dプリンタは、これまでFDM方式が主流だったが、安価な光造形方式の製品が現れたことで、選択肢が広がった。光造形方式にも、SLA(Stereolithography Apparatus)と呼ばれるレーザー照射方式とDLP(Digital Light Processing)と呼ばれるプロジェクター方式があり、後者は、紫外線をLCDパネルに表示されるパターンによって遮ることで、必要部分だけを硬化させる仕組みだ。
スマートフォンの普及によって小サイズで高精細なLCDパネルのコストが下がったことにより、特にDLP方式の製品は価格破壊が著しく、SparkMakerも、クラウドファンディング時には200ドル以下、その後は300ドルを切る価格で販売されている。
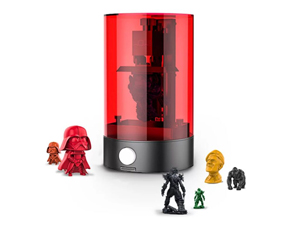
写真1:SparkMakerの筐体。(クリックで拡大) |
 |
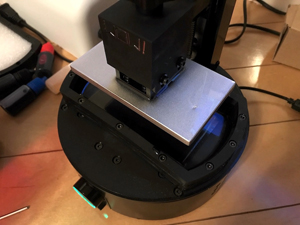
写真1-2:SparkMakerは、同じ光造形でもDLP方式を採用し、液体樹脂タンクの下面から紫外線をLCDパネルによって照射することで硬化させる仕組みになっている。(クリックで拡大) |
DLP方式の光造形では、LCDパネルの面積内であれば造形物の多少にかかわらず造形時間は一定となる。バッジは数十個作る必要があったため、一度に4つのバッジを造形することで時間短縮をはかった。
また、一般的な光硬化樹脂は造形後にアルコール洗浄しなくてはならないが、SparkMakerは水洗浄が可能な液体樹脂を開発しており、これを用いて造形した。
また、光硬化樹脂は、造形後もまだ完全な硬度に達しないので、全面的に紫外線を照射して固める必要があり、この工程は「キュア」と呼ばれる。キュア専用の装置も別売りされているが、筆者は同じ原理で硬化させるジェルネイル用の安価な紫外線照射器を愛用している。
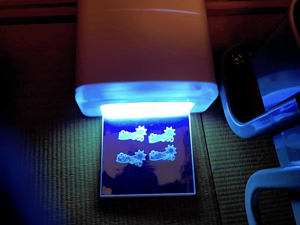
写真4:造形後に、全体に紫外線を照射して硬化を完全なものとする処理は「キュア」と呼ばれる。筆者は、ジェルネイル用の安価な紫外線照射器を利用している。(クリックで拡大)
|
 |
|
光硬化樹脂そのものは透明で、事前に専用の染料と混ぜることで着色も可能だが、今回のバッジは、ベース部分と文字部分で色分けしたいこともあり、後からスプレーペイントとマーカーで色付けすることにした。
最終的に、バッジの裏側にアクセサリー用の安全ピンを取り付けて無事に納品となり、学生さんたちからも好評を得ることができた。
DLP方式は、FDM方式と比べて難しい印象を持たれている方も多いように思うが、実際には、より失敗が少なく、精度も出しやすく、モノによって造形時間も短くて済むメリットがある。
一方で、造形サイズが大きくなると、プリンタ自体もFDM方式のほうが安価であったり、フィラメントも液体樹脂よりコストがかからず、造形後の洗浄や乾燥の手間もないなど、扱いやすい面もある。
今後も、趣味や実用のために、FDM方式とDLP方式を使い分けながら、さまざまな3Dプリントの応用を試みていくつもりだ。
短い間ではあったが、ご愛読ありがとうございました。
(2018年11月7日更新)
|