●西陣織の道具がなくなる!
第10回の北村茂之(庄松屋)さんからご紹介いただき、このリレーコラムを書くこととなりました足立と申します。Fusion 360という3D CADがつないでくれた不思議な縁ですが、今回は3Dプリンタと伝統産業についてお話させていただきます。
事の発端は以前からの知り合いであった西陣織の職人様からのご依頼でした。
「足立さん、ちょっとこの部品、その機械で作れませんか?」
2年ほど前、ヤフオクで購入した卓上CNCフライスを使ってFusion 360のCAMの練習をしていた時に、その機械を見て声をかけていただきました。
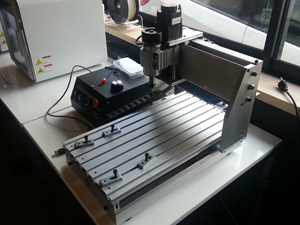
ヤフオクで購入した卓上CNCフライス。(クリックで拡大) |
 |
|
その職人様は中村さんとおっしゃる方で、京都で500年以上続く西陣織という伝統的な絹織物の織り手さんです。作れないかと相談いただいたのは中村さんが普段使われている杼(ひ)という部品で、織物に緯糸を供給する役目を果たすものです。
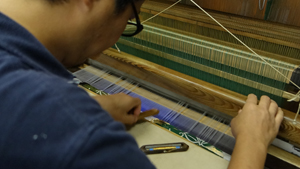
中村さんと機織りの様子。(クリックで拡大) |
 |
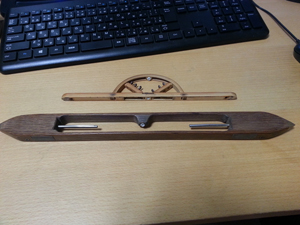
西陣織に使う杼。(クリックで拡大) |
この杼も織物と同じように一品一品手作りで作られているのですが、その杼づくりをされる職人様が京都にはもう1人しかいないような状態になっており、もしこの方が廃業されると京都では杼を供給してくれる工房がなくなってしまうとのこと。これには中村さんも非常に危機感を持たれていました。
●何だかうまくいかないぞ
最初はかなり簡単に考えていました。大きさも手持ちのCNCフライスで削れそうだし、形もそんなに複雑じゃないしと。
でも本物の杼と同じような硬い木を削ろうとすると私が持っている機械ではパワーが足りず少しずつしか削ることができないとか、4面加工でそれなりに仕上げようと思えば結構きっちりとした位置決めをしないといけないとか、いろいろと問題にぶち当たってしまいました。
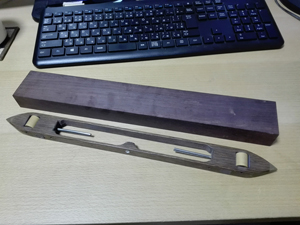
最初はこの木材から削り出そうとした。(クリックで拡大) |
 |
|
時間がかかりすぎる。いや、やろうと思えばいくらでも段取りを考えて作ることはできるのですがあまりやりたくないなぁと。他に方法はないだろうか。
●3Dプリンタで時間を生み出す
今回取り組んだ杼の再生に限らず、およそ開発と呼ばれる活動には必ず「試作品を作って実際に試してみる」というステップがあるかと思います。それも開発の節目ごとにそれぞれ違う目的でさまざまな数量で作ったりします。
特に開発の初期段階では、そのテーマにどういった問題点があってどれほど難しいのか明確にしておく必要があります。そういった場合にとにかく早く試作を作ってガンガン試すことができると問題点の抽出がスムーズに行えるわけです。
今回の取り組みでもとにかく早くモノを作って試したかったのですが、最初の1個を作るのに固定治具の仕様も考えて本体も含めて加工データを作り、長時間かけて卓上CNCフライスで削っているようではそのスタートすら切れません。時間をかけてモノづくりしてもいいけどそれは仕様が固まった最終段階の話かなと。さて困りました。気楽に引き受けたのはいいけれど、当初の目論見は外れてしまい、ちょこっと木を削って一丁上がりとはいかなくなりました。
こうなるともうアレです。データさえ作れば後は勝手に造形してくれる3Dプリンタを使うしかありません。基本的に機械に張り付いて段取りしないといけない卓上CNCフライスに比べて、3Dプリンタは人が関与する度合いが格段に低くて済みますから。
●商用サービスを使い倒す
3DプリンタにはFDM方式(熱溶解積層方式)やSLA方式(光造形方式)などがありますが、今回はSLS方式(粉末焼結積層方式)を使うことにしました。
SLS方式の3Dプリンタはまだ価格が高く、個人レベルで維持管理できるようなものは出回っていないようです。今回はDMM.makeさんの3Dプリントサービスを利用することにしました。
DMM.make 3Dプリント
https://make.dmm.com/print/
選択した素材はナイロンです。実は今回の杼以外にもさまざまな部品をDMM.makeさんで作っているのですが、使う素材はほとんど毎回ナイロンです。
ナイロン焼結の特徴はこんな感じです。
・靭性が高いためスナップフィット形状を作りやすく、タッピングネジの下穴も形成しやすい
・強度が高く力が加わる部分でも壊れにくい
・造形後の表面はザラザラ感が残るが、紙ヤスリで磨くとかなりのところまで平滑面を得ることができる
・最小0.8mm程度の薄肉部があっても造形可能
・積層した粉が造形した構造物を支えるためFDMやSLAのようなサポート(支柱)が不要
・粉の排出口さえ確保できればかなり複雑なアンダーカット形状でも造形可能
扱う対象が樹脂部品であるならば、ナイロン焼結は試作用途として非常に優れた性質を持っていると言えるでしょう。それからDMM.makeさんのナイロン焼結は他の素材に比べて非常に安価であることも付け加えておきます。
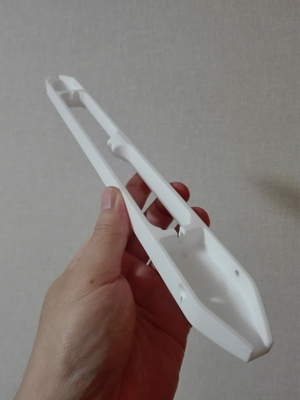
3Dプリントしたナイロン製の杼の本体(クリックで拡大) |
 |
|
●デジタル職人とは
本体のボディを3Dプリンタで作ることを決めたついでに、オリジナルから設計仕様を変えてもっと簡単に組み立てられるようにしました。
オリジナルの杼はノミやカンナ、ヤスリやノコギリ、その他多数の手作業で使う工具類、据え付けのボール盤や木工旋盤やグラインダなどを使って作られています。それから音を出して作業できる場所が必要です。杼の重量を調整するために鉛を使ったりしているので、鉛を溶かす熱源と道具も必要になります。そして何より手作業が基本となっているため、まともなモノを作り出すのに長年にわたって修行しなければいけません。
私が設計した杼はすべて3D CADで設計してデジタルデータとして存在していて、PCからWebを介して部品発注と入手が可能です。組み立ても紙ヤスリとドライバーと少しの接着剤があれば素人でもできてしまいます。作る場所も事務机1つと椅子があれば十分です。杼が壊れたら破損した部品だけを自分で取り換えることも可能です。織機の中での杼の動作を理解して設計し3Dモデルに落とし込むという作業は必要ですが、それでも何年も修行する必要はありません。
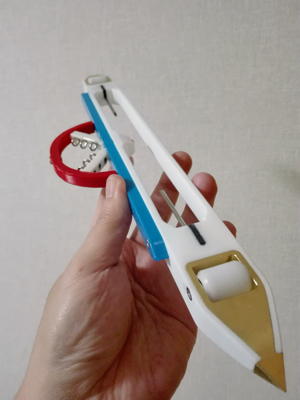
新しく設計した西陣織の杼。(クリックで拡大) |
 |
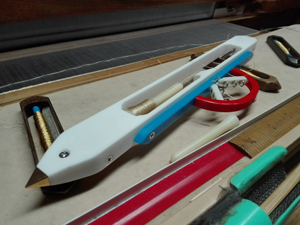
新しく設計した西陣織の杼。(クリックで拡大) |
これが何を意味しているのか、今何が起きているのか。
ひょっとしたらやっと職人的なノウハウをデジタルなデータとして残せる時代がやってきたのかもしれません。必要な機能を理解して部品の形に落とし込むという作業は、杼の職人様も3D CADで設計している私も本質的なところでの違いはないと思います。違うのはその設計情報をどのような形で残すのか、それに基づいてどうやってモノを再生産するのかというところではないでしょうか。
今の時代の便利な機械に合わせて部品の仕様を変える。設計情報は個人の頭の中ではなく、3Dデータとしてコンピュータの中に残して設計者本人でなくとも理解可能な形にする。3Dデータを使ったら誰が作っても同じものができ上がってきて何度でも再生産できる。
私が杼の職人様のノウハウをすべてデータ化できたかと言うと決してそんなことはありません。せいぜい入り口に立ってほんの少し中を覗いたぐらいと言うのが本当のところです。それでも何だか次の時代の職人仕事の在り方が1つ見えてきたんじゃないかなと感じています。
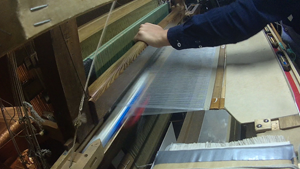
3Dプリントした杼で機織りする様子。クリックでMP4動画が再生されます。
|
 |
|
●3Dプリンタの未来
私が3Dプリンタに求めるものはスピードです。作るのは技術開発に使う試作品がほとんど。完成に近い製品というよりも基礎技術データを取ったりして設計の根拠系の構築に用いる部品が多いですね。だから色とか見栄えとかは二の次でとにかく爆速で部品を手に入れたい。
素早く部品が手に入るということは新しいアイデアを次から次へと試せるということです。完成した設計案の良し悪しを確認するのではなく、設計初期段階でのアイデア評価装置として3Dプリンタを使えないでしょうか。例えばジェネレーティブデザインで吐き出した設計案を片っ端から造形する爆速3Dプリンタとか。何だかわくわくしますね。
次回の執筆は小原照記さんです。
(2018年12月12日更新) |