今回、石渡さんからのご紹介でコラムを書かせていただけることとなりました、MARUTTOYSのMiZと申します。メカ系の造形をメインとしている造形作家です。最近では出力キットをメインで販売しています。
●3Dプリンタとの出会い
なんとなく無料なのでダウンロードしたFusion360にドはまりしました。そしてデータを現実世界に出力したいという思いから「UP mini2」というFDMプリンタを購入。購入した機種が良かったのか初手から呆気なく出力に成功して「なんでも作れるのでは!」と心が踊ったのをよく覚えています。最初はスマホケースや自転車のライトマウントなど実用的な部品を出力して遊んでいました。
しばらくするとデータを作る技量も上がり、複雑な形状のデータが作れるようになります。もともとガンプラやアクションフィギュアが好きだった私は、メカの可動フィギュアのデータ制作をするようになります。
●初めて3Dプリンタを活用した造形
FDMプリンタのフィラメントはABSを好んで使っていました。適度な弾力と強度があって最初の方に出力していた実用品にはもってこいでした。ABSの樹脂の特性はアクションフィギュアなどの可動部品にも適した素材です。そこでボールジョイントやネジ式稼働などABSだからできる構造の出力品メカを初めて造形、出力をしました。
部品単位で何度も出力とデータの調整を繰り返して関節の渋みや強度の確認ができる3Dプリンタは、今までアナログ造形しかしてこなかった私には衝撃的でした。アナログ造形なら3ヶ月近くかかったであろう作品を、データ制作から出力までトータル1週間という速度で行えたのは本当に驚くべきことでした。その後変形機構を組み込んだより高度な作品を制作したりしました。
これらの作品制作で出力方向によって強度が変わったり、出力の積層向きによって品質が変わること、などなど今後に生かされる知識を吸収することができました。
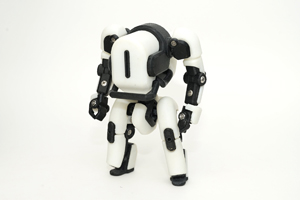
2017 年に制作した3D プリンタによる最初の作品。(クリックで拡大) |
 |
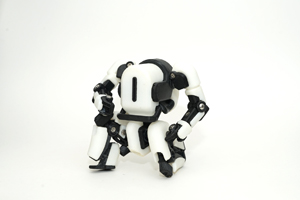
各部がネジとボールジョイントにより可動。(クリックで拡大)
|
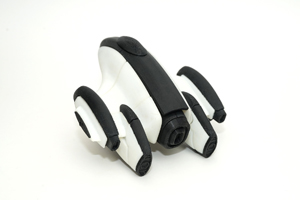
2017 年、変形機構を盛り込んだ作品。(クリックで拡大) |
 |
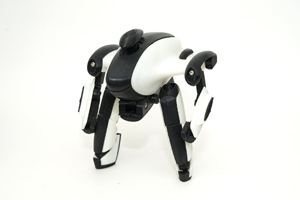
胴体はリンク機構によりワンアクションで3 箇所が動く。(クリックで拡大)
|
●3Dプリンタを使った作品販売
「自分の作った作品が世の中で勝負できるのか?」。考えていたより3Dプリンタを使った造形が思い通りに進み、謎の自信が溢れてきた私はワンダーフェスティバルでディーラーデビューを考えるようになります。
販売する作品のデザインは難航し、半年ほどの時間を要しましたが、なんとか形にすることに成功しました。そこで生まれたのは「MAMORU」と「TAMOTU」です。FDMの3Dプリンタで出力されたABS製のフレームとウレタンレジンキャストの外装の異素材を組み合わせたキットが誕生しました。
FDM製の部品はどうしても積層痕が目立つのが気になり、パーツを磨きシリコンで複製したレジンキャストに置き換えました。ネジ関節のフレームはABSの出力品で、難しい穴が開けが不要でドライバーがあればネジを締めていくことができ、パーツの歪みが少ないので比較的組み立てやすく、素材を生かした粘りのある関節を実現しました。
それとすべてをレジン複製してしまうと複製を外注している私にはコストが高くなってしまいます。一部を出力品に置き換えることにより製造コストを大幅に下げることにもつながりました。このあとFDMとレジンキャストの異素材混合キットは「NOSERU」、「HAKOBU/RIKU」と続いていきます。
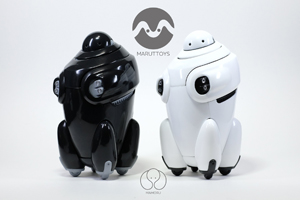
2018 年「MAMORU」。(クリックで拡大) |
 |
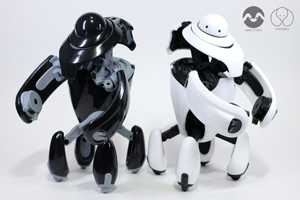
簡易的な変形機構がある可動作品。(クリックで拡大)
|
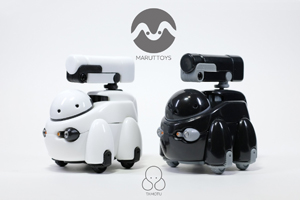
2018 年「TAMOTU」。(クリックで拡大) |
 |
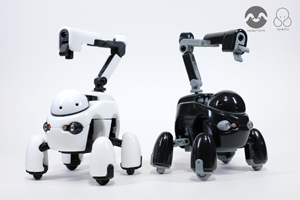
簡易的な変形機構がある可動作品。(クリックで拡大)
|
●光造形3Dプリンタの導入
FDM機の魅力は強度があったり、大型な出力ができたり、後処理が比較的楽など利点も多くあります。ですが積層痕が目立ったり、小さい造形のディテールの再現が難しい(機種によっては可能)などの問題点があります。
それを解消するために導入したのが低価格光造形3Dプリンタの先駆け的存在「ANYCUBIC Photon」です。低価格のDLP式の光造形機が登場する前は、光造形といえば外注でめちゃくちゃ高い印象でした。それが5万円程度の本体代金と1万円以下の樹脂代で印刷できるのは破格だと感じました。
ただ最初に使ったレジンが水洗いレジンだったのが良くなかった…。当時の水洗いレジンはピーキーな性能で印刷するのが難しく、かなり苦戦しました。出力後の保存状態にも気を使う必要があり、湿気により樹脂の変形や破損がなかなか厄介でした。ただそれでも精密なディテール表現や表面の滑らかさには将来性を感じました。
その後ANYCUBICの純正レジンを使い、上等な出力結果を得ることに成功しました。ちなみに現在の水洗いレジンは油性レジンに近い性能までレベルが上っているそうです。
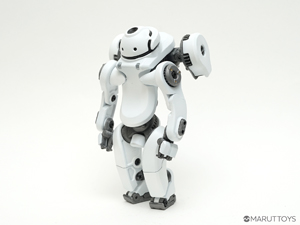
2019 年「TAMOKU」。(クリックで拡大) |
 |
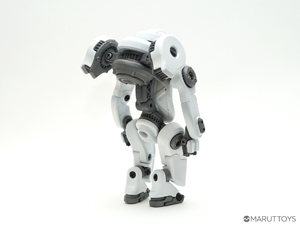
FDM 製のフレームと光造形のミックス。
光造形出力品が割れるなど安定性がなく販売を断念。(クリックで拡大)
|
●光造形出力品キットの販売と得た知見
Siraya Tech製のレジンと、ELEGOOの3Dプリンタの導入により精度の高い出力品を安定して出せるようになってきました。出力品を野外で数ヶ月放置して経年劣化を確認したり、ある程度の高さから落としてみて破損テストをした結果、ガレージキットとして販売しても問題ないという考えに至りました。
今回も異素材混合のキットで、大きい部品をレジンキャスト複製品、細かな部品は光造形の出力品にしたキット「NASTER」を制作しました。まだ3Dプリンタで大量複製するには経験不足だったので、大型の部品をウレタンレジンキャストの業者複製とすることで私自身の負担を下げようという理由から異素材キットになってます。
今回のメカは非可動の固定キットなので、ディテールや造形に集中できるようになり結果的に光造形機の利点でもあるディテールの再現性をうまく活用できました。
そしてNASTERを制作するにあたってもっとも収穫があったのが部品の一体化です。通常レジンキャストのシリコン型での複製は、複雑に入り組んだ形状のような逆テーパーが大量にある部品は通常複製が不可能です。それを解消するためにはパーツを適切な箇所で分割するなどの作業が必要でした。光造形出力品はそういった分割などの処理が不要なので、複雑な形状が1つのパーツとして出力することができます。パーツが少なくなり組立工程が減り、組立時のミスが削減できるため、私も購入者もキット組み立てのハードルは下がったように感じました。
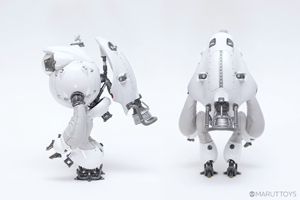
2021 年「NASTER」。(クリックで拡大) |
 |
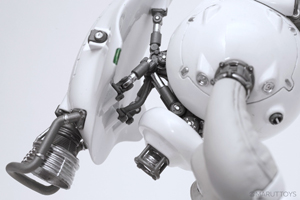
複雑に入り組んだ背面のシリンダーはすべてワンパーツ。(クリックで拡大)
|
●光造形出力品キットがメインに
NASTER以降は光造形出力品のキットのみを販売していきます。出力品は形状の自由さ、量産も必要な分だけすぐに自宅で量産できるフットワークの軽さ、レジン複製に比べて生産コストを抑えれることなどさまざまなメリットがあります。もちろんデメリットはありますが私には光造形出力品でキットを販売するほうが現状向いているようです。
出力品販売を重ねていくにつれて、出力品でしか実現できない形状のキットが増えてきました。パーツ数を2パーツまで減らした「レインコ」、そもそもワンパーツで出力された組立不要の「ルドリウスミニ」など、光造形出力でないと実現できない作品を販売していきます。
そして光造形出力品の強度では難しかった可動作品を、ゴムライクレジンや高靭性のレジンの登場によって販売することできました。光造形の出力品の弱点は強度でしたが上記の素材を適材適所に使用することで折れにくく、すり減りにくい可動作品にすることに成功しました。3Dプリンタの性能もかなり上がり、なおかつ低価格で品質や豊富な種類のレジンが増えてきたので導入当時よりできることが大幅に増えてきました。

2021 年「NASTER」。(クリックで拡大) |
 |
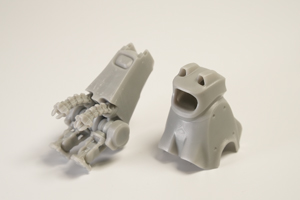
複雑に入り組んだ背面のシリンダーはすべてワンパーツ。(クリックで拡大)
|
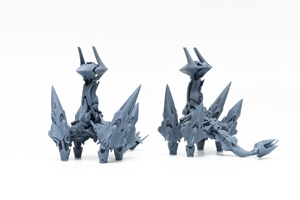
2023 年「ルドリウスミニ」。(クリックで拡大) |
 |
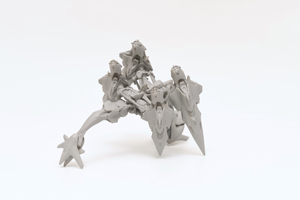
ワンパーツ、下面にサポートを集中させることで処理せずとも見栄えを良くした。(クリックで拡大)
|
●今後3Dプリンタに期待すること
やはりウレタンレジンキャストの複製品と比べると強度や耐用年数などがいま一歩届いていないと感じますが、差を埋められるようになるまでそんなに時間はかからないかもしれません。
それと温度や湿度の違いでレジンの安定性が揺らぐこと、筐体の精度がバラけているのでZ軸の精度などが足りていないなど、さまざまな理由から出力が失敗することがあります。欲を言うと湿度や温度を調整する機構を持った3Dプリンタや、Z軸のボールねじやステッピングモーターを工業用のグレードにした20万円クラスの機種があると嬉しいですね。
一番求めているのは、ボタンを押せば誰でも同じ品質で出力される安定した3Dプリンタです。年々レジンの性能も3Dプリンタの性能も上がってきているので、いつか実現できると信じています。今後の発展が本当に楽しみな業界です。
次回の執筆者はYoshi.さんの予定です。
(2023年10月10日更新) |