今月はCAEと工業デザインの関係を考えてみたいと思います。というのも、CAEツールは工業デザイナーだけでなく、いわゆる「工学」を主たる業務とするメカの設計者にとっても、多くの場合新しいツールであることが多いからです。
CAEツールは、多くの他のテクノロジー同様にうまく使いこなすことで単に仕事を効率化するだけではなく、場合によってはクリエイティブな発想のヒントにつながることもあります。
●そもそもCAEツールとは
そもそもCAEは、Computer Aided Engineeringの略でコンピュータ支援による設計などとも訳されます。ただ、CADもコンピュータ支援による設計なので、この2つはどう違うのでしょうか。
筆者の定義としては、CADは主として形状を作り上げていくための道具で、CAEはそれが工学的に求める性能を発揮するかどうかを検証する道具です。具体的にはどのように検証するのでしょうか。それは、コンピュータ上でその挙動をシミュレーションなどをして検証します。そのため、CAEツールのことをシミュレーションツールなどということも多いのです。
CAEで挙動を検証できる分野はさまざまで、部品や筐体などが壊れないか、あるいは過大な変形をしないかどうかなどを検討する「構造解析」、その物体の周囲を空気や液体などの流体がどのように流れるのかを検証する「流体解析」、熱がその物体にどのように影響を与えるのか検証する「熱解析」、それ以外にも音響や電磁場の解析など、範囲は実に多いのです。
この中でももっともポピュラーなのが構造解析なので、CAEと言えば最初に構造解析のことを思い浮かべる人も多いでしょう。構造解析では、外部から荷重がかかった時にどのように変形するかを確認するとともに、物体内部に発生する力、すなわち応力を確認するので、応力解析と呼ばれることもあります。
通常は、このような検討は実際に製品に使用される材料を使って試作をしないと確認することができないので、それをコンピュータ上でできることは大きな効率化につながります。なにしろ、実物を作る前に手直しができるわけですから。
このような道具は製品のエンジニアリングに直接関わらないとしても大いに役にたちます。工業デザイナーであっても、製品によっては意匠面だけに責任を持つだけではなくて、自分のデザインしたその形自体が製品の強度に影響を与えますし、同じ形であっても材料の選択も製品のパフォーマンスに大きな影響を与えます。
例えば、このようなことをあらかじめ考え、検証しながらデザインをしていくことで、それがエンジニアリング的に問題があって意匠に関わるような変更をしなくてもよくなるかもしれません。うまく使えばとても便利な道具なのです。
●手が出しやすくなったCAEツール
ところが、CAEツールを使いこなすには、一般的に3つのハードルがあります。1つ目が工学的な専門知識を持っていること。2つ目はCAEツールの使いこなし自体が難しいこと。そして、もう1つは、一般的にソフトの価格が高価であることです。
1番目のハードルですが、確かにCAEに関わる知識は難しいものがあるのですが、別に自分で解析ソフトを作るわけではありません。また、解析の中でも非線形と呼ばれる、より難しい挙動も扱う必要があるケースも多くはないでしょう。その場合、解析の設定をするためと最低限の結果が評価できるくらいのことだけ分かれば大丈夫です。もし、あなたがデザイナーでエンジニアリングの評価そのものに責任を持っていなければ、最終的には設計者に任せることができます。
2番目のハードルですが、本格的な「解析専任者」が使用する解析ソフトは非常に高機能であるがゆえに多くの設定ができますし、細かな調整ができるのですが、「電卓代わりに」解析をするのであれば、そのような難しいことは必要のないソフトが出てきています。
また、従来の解析ソフトは、解析のための「メッシュ」とか「節点」を扱わなければいけないのですが、CADに付属しているソフトであればCADで作成した形状だけで設定から評価まで行うことができるので、2番目のハードルもだいぶ下がっています。
最後のハードルですが、非常に安価かつ本格的な機能を持つ解析ソフトが登場しています。その代表的な例がオートデスク社のFusion 360です。同ソフトは、一般的にはCADとして認知されていますが、シミュレーション機能も比較的本格的なものが入っていて、少なくとも「電卓代わりに」解析をするには十分すぎる機能が、年間40,000円以下の価格で使用できてしまいます。モデリングにFusion 360を使っていなくて他の3Dモデラーを使っていても形状をインポートして使用することができるのでCAEツールのみとしても使用することができます。
●解析の流れ
例えばRhinocerosで下に支持のついた棚板を作ってみます。
RhinocerosのネイティブデータはFusion360でインポート可能なのでそのまま読み取ります。
この形状に壁への固定の条件や何かものが置かれた時の荷重の条件、それにどんな材料が使用されているのかの定義をします。ここではこの棚板はABSのプラスチックでできていて、約10キロの荷重がかかっているものとします。
解析を実行すると最初に表示されたのが安全率です。安全率とは壊れる強度に対して現在の状況はどうかというものを示すもので、1以下だと破壊されてしまう状況で、数値が高いほど安全です。ここでは安全率が14を超えているのでとても安全なのですが、数値が高すぎると安全すぎて過剰設計という状態です。
つまり無駄に強度がありすぎる状態で、材料コストや製品の重量を考えるともっと弱く作っても大丈夫です。
そこで、元々5mmあった棚板の肉厚を、1.5mmにしてみました。
その結果、最大の安全率が5.41にまで小さくなりました。一般に多くの工業製品では安全率が3から6くらいが適切とされることが多いですので適切なレンジに収まりました。
最大の変位量も0.13mmとほぼ目視では確認が難しいほどの変形量なので、このように材料を大胆に削ってしまっても安全であることが確認できました。
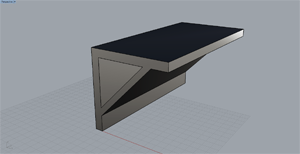
図1:Rhinocerosで下に支持のついた棚板を作る。(クリックで拡大) |
 |
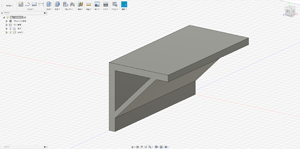
図2:RhinocerosのネイティブデータをFusion 360にインポート。(クリックで拡大) |
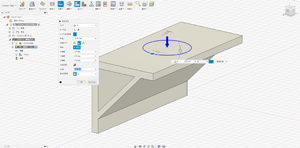
図3:ABSに約10キロの荷重がかかっているとする。(クリックで拡大) |
 |
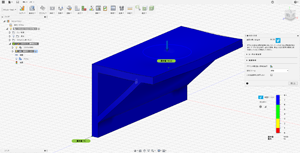
図4:安全率が14を超えている。(クリックで拡大) |
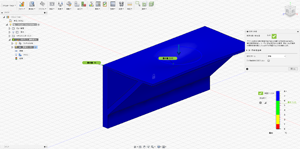
図5:棚板の肉厚を1.5mmに変更。(クリックで拡大) |
 |
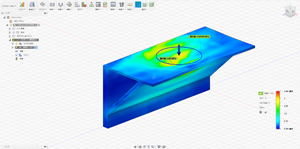
図6:最大の変位量も0.13mmとほぼ目視では確認が難しいほど。(クリックで拡大) |
どうしても、人は自分はある環境に馴染んでしまうと例えば従来の道具にこだわって新しい道具を避けてしまいがちになります。しかし、最近のソフトは初心者にもとても使いやすくなっています。
本当に機能するものを作るために、少し新しい道具でシミュレーションにチャレンジしてみてはいかがでしょうか?。
次回は7月中旬掲載予定です。
(2018年6月18日更新)
|