●FDM方式(FFF方式)のメリット
前回は、さまざまな3Dプリンタの方式とそれらの特徴、どのように使い分けていけばよいのかを筆者の経験に基づいて簡単に述べてみた。今回からは、数回に分けて各方式について、もう少し詳しく説明していきたい。
ということで、最初に「FDM方式」あるいは「FFF方式」と呼ばれる種類の3Dプリンタについて述べてみる。FDM(Fused Deposition Modeling)方式は、熱溶解積層法などとも訳されることがあるが、簡単に言うと樹脂をノズルで溶かして積み上げていく方式のプリンタのことである。
パーソナルユースで使える3Dプリンタというとほぼこの方式を指す。最近では、60万円も出せば、かなり高機能の光造形方式の3Dプリンタが手に入るが、比較的安価なものというと現在でもFDM方式であることは間違いない。筆者は、デアゴスティーニ社で出していた「週刊マイ3Dプリンター」の本誌監修をしていたが、このシリーズで組み立てたのも、やはりFDM方式のものだ。
かつては、安価なFDM方式の3Dプリンタというとホビーユースを考えても品質的に疑問がある場合も少なくなく、機械自体の信頼性が低いものが多かったのは事実だ。しかし、現在では20万円台の同方式の3Dプリンタであれば、問題なく試作に使うことができる機械も多い。実際、筆者は自分の業務において「Zortrax」という3Dプリンタを所有しているが、3D CADで設計をしたあとに形状などの確認をする際に頻繁に使用している。筆者の場合には、光造形方式の「Form2」と呼ばれる3Dプリンタも利用しており、これらの2台を使い分けながら出力をしている。
●FDMと光造形を比べると
ただ、これらの2台を比較すると、現在、使用頻度が高いのは、FDM方式のZortraxの方だ。単にでき上がりの形を見るだけであれば、どちらの方式を使用してもかまわない。もし、どちらでもよいのであればFDM方式の方がコストの面で有利だ。
FDM方式では、どうしても微細な形状の表現は難しく、潰れてしまう傾向にあるし、積層痕もはっきりと目立つ。したがって、ジュエリーやフィギュアなどには不向きで、筆者もそのような詳細な形状が要求される場合には光造形方式を使用する。その一方で、それほどのディテールが要求されない、かつ大きめの形状であれば迷いなくFDM方式を使用する。
例えば、Form2の場合、もっとも安価な一般的なレジンで1リッター18,800円程度の材料費がかかるが、Zortraxの場合には800グラムで5,000円程度と価格面でかなり有利だ。さらに手間の面でもFDM方式は有利だ。光造形方式の場合、液体の材料を扱わなくてはいけない上、出力が終わってもIPAなどのアルコールで洗浄し、さらに二次硬化も必要であるなど慣れても案外面倒だ。それに対してFDM方式は出力をしてしまえば、あとはサポート剥がしてそれで終わりである。材料もワイヤ状の巻物の形で提供されているので圧倒的に楽だ。
FDMは詳細な形状の再現性が低いといっても、ちょっとしたネジ程度であれば、嵌合も含めてきっちりと再現できる。さらに表面の積層痕が気になる場合には表面を紙やすりで磨き、さらにサーフェイサーなどを吹けばかなりきれいになり、塗装も可能だ。
もう1つ言えるのは材料物性だ。材料物性のバリエーションから考えると一般的に光造形方式のほうがバリエーションが多いのは確かだ。中には歯科技工用のものやキャスト用のレジン、耐熱レジンなどさまざま。
それに対してFDM方式の場合にはABSやPLAが多いのは事実だ。その一方で光造形方式は、○○ライクというような機械的な特性を模した形になるのに対して(ABSライクなど)、FDM方式でABSといえば本当にABSである(安価なものだと品質に怪しいものがあるが)。ABSは一般的な製品でも多用されるエンジニアリング樹脂だが、材料特性の観点からもFDM方式のほうが良い場合もある。
したがって、あえてコストのかかる光造形方式を使用しなければいけない場合でなければ筆者は、FDM方式で出力するし、試作の観点からもそれで問題はない。
●出力する際の方向が大切
FDM方式に限らず、どの方式でも出力にはある程度のノウハウが要求される。方式を問わずもっとも気にしなければならないのが、出力の向きだ。
強度の面から考えると積層した時のレイヤーは剥離することも考えられるので力の方向によっては材料の本来の強度が発揮できない場合がある。力の掛かる機能部品の場合には、そのあたりのことを考えて出力時の向きを考える必要がある。
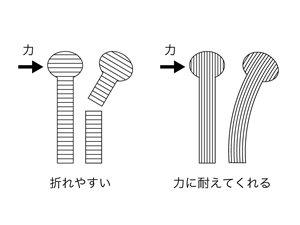
図1:力の方向と積層レイヤー方向の関係。(クリックで拡大)
|
 |
|
次に考えなければいけないのが形状の再現性だ。例えばある物体に丸い穴が空いていることを考えてみる。穴の向きが垂直になるように出力できれば、穴の形はほぼ真円になるが、横倒しの場合には、特に小さな穴の場合には少し潰れて楕円になることがある。これは穴ではなくて丸棒の場合にも言える。
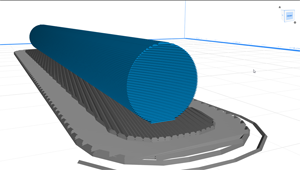
図2:丸棒を横に倒した場合。棒の軸と直交する方向に力がかかる場合には比較的強度を保つが断面が真円にはなりにくい。(クリックで拡大)
|
 |
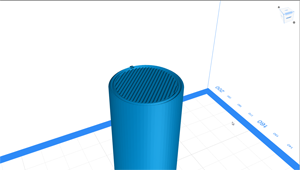
図3:丸棒を立て場合。軸と直交する方向に力がかかると弱いが断面は真円に近い形状の再現度がある。(クリックで拡大)
|
●サポートの位置と反り
サポートの位置も重要だ。サポートがつく面はサポートを除去したあとに荒れてしまうことは否めないので、大事な面はサポートがつかないように配置する必要がある。さらに、下手な場所にサポートをつけてしまうと除去すること自体が困難だったり、サポートを外す時に詳細な形状まで一緒に剥がしてしまったなどのことがある。
熱による反りもFDM方式では避けて通れない悩みだ。特に大きくて薄い形状の場合には、出力中に造形のプレートから一部が剥離してしまって反り上がった形状になったことはよくあるトラブルだし、ちゃんと出力できた場合でもたわみやすいものだ。できるだけ、この反りの悩みにひっかからない向きを考えることも重要だ。
どの向きで出力するのかということを考えるにあたって、これらの要素を同時に考えて決定する必要があるというわけだ。
●FDM方式を使う際のちょっとしたノウハウ
最後に出力にあたっての簡単なノウハウを示してみたいと思う。
1つは剥離防止のノウハウだ。大きめの物体の出力の場合、図に示すような角の部分が剥離することはめずらしくない。そこで、このような場合には過度のところにこのような丸い形状をモデリングの段階で付け足しておいて出力後に切り離すと剥離がしにくかったりする。ただし、糊代の部分の形状が変わってしまうのであとで切り離して磨くなどの後処理も必要なので、他の手段がうまくいかない時の最後の手段とも言える。
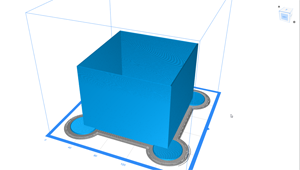
図4:ソリ防止の一例。(クリックで拡大) |
 |
|
造形の際の中身の密度も大事だ。FDM方式では中身を完全に詰め詰めにするのか、ハニカム状などに中を空洞にして軽くするのかなどを選ぶことができる。強度が要求される場合には中身を詰めたほうがよいが、一方で大きなものだとかえって反りが発生することがある。強度が要求されないのであれば密度は小さいほうがよい場合がある。
最後に肉厚の問題だ。例えば薄板のような形状の場合だと、寝かせて出力するよりも立てたほうが反りなどに悩まされない。立てても案外倒れたりもせずに安定して出力することができる。ただ、あまりにも肉厚が薄い場合(例えば1.2ミリなど)の場合には若干の注意が必要だ。多くのFDM方式のノズル径は0.4ミリだ。したがって肉厚が0.4ミリの等倍であれば、しっかりと肉が詰まった形になるが、例えば0.9ミリだったりすると、スライサーによっては0.1ミリの隙間ができてしまう。肉厚が2ミリくらいまでなら0.4の倍数の肉厚にすると良いといえる。比較的高価な機械で専用のスライサーが用意されている場合には気にしなくてよいが、フリーの汎用スライサーを使う場合には注意したほうが良い場合がある。
このようなノウハウに習熟していくと、FDM方式はかなり使える方式であることが理解できる。。
次回は9月中旬掲載予定です。
(2018年8月20日更新)
|