●アメリカの美術大学時代からGENKEI設立まで
--:MagnaRectaのお話をうかがう前に、まずこれまでの歩みについて振り返っていただけますか? 加藤さんが3Dプリンタに関わったきっかけからお願いします。
加藤:私が3Dプリンタに最初に触れたのは、アメリカのパーソンズ美術大学の学生時代に遡ります。2007年頃ですね。パーソンズで私はプロダクト/インダストリアルデザインを専攻していました。ここでは社会の出来事に対応したデザインのあり方、考え方を学びました。例えば何かの出来事が発生した際、デザインの対象物が、薬になったりバイクになったり椅子になったりと変わるのですが、出来事の起承転結を考えた結果のデザインという考え方です。
パーソンズでは、さまざまな作品や手作りのモックアップなどを制作していたのですが、それらすべてを2009年の卒業当時に手違いで処分されてしまいました。それで就職活動用のポートフォリオを作ることができなくなってしまい、どうしようというときに、2、3年前に知ったRepRapプロジェクトを思い出しました。
オープンソースであるRepRapであれば、300~500ドルで3Dプリンタを作ることができるということで、処分されてしまったモックアップなどを3Dプリンタで出力しようと考えました。ちなみに、私は理系ではなかったので、オーム、ボルテージ、アンペアって何? というレベルだったんです(笑)。
当時私は、ブルックリンに隣接するマンハッタンに住んでいたのですが、ちょうどその頃、川を渡ったところにMakerBot社ができました。そしてザック・ホーケン、ブレ・ペティスらが作った木製の組み立て式の799ドルの3Dプリンタ「Cupcake CNC」が発売されました。
私はRepRapプロジェクトで1から3Dプリンタを組み立てようとしていたのですが、結局、Wikiの説明も理解できず完成に至らなかった(笑)。なにしろRepRapはミニ四駆のような組み立てキットかと思っていたら、ニクロム線から自分で調達しなければならなかった。美術大学でしたので筐体を作ることは得意だったのですが、ともかく基板が分からない。
そこでMakerBotの「Cupcake CNC」を買って、その基板をRepRapマシンに入れてみることにしました(笑)。それが、なんと動いてしまったのです。ただ、RepRapはメンデル型と呼ばれ造形サイズが20センチ角なのですが、「Cupcake CNC」は10センチ(5インチ)角しか動かない。そこでソフトをいろいろ探ってみて、プーリーの径、Step by Unitをファームウェアで調整すればよいことなどが少しずつ分かってきました。
そこからArduinoを理解することになりました。ArduinoはセンサーやLEDを動作させるオープンハードとソフトのシステムですが、Arduinoを3Dプリンタに特化させたシールドから、今でもよく使われる「RAMPS」という基板が生まれたわけです。ようするに3Dプリンタは機体本体とファームウェアを入れたArduinoベースの電子基板群が揃えばできるようになったわけです。
--:そしてポートフォリオを持ってアメリカで就職活動ですか?
加藤:結局、就職活動時に制作物のポートフォリオは間に合わなくて、CGのレンダリングをまとめたポートフォリオだけでニューヨークの建築事務所に就職できたのですが、3Dプリンタには開拓時代から関わることができたので、就職後もずっと趣味で3Dプリンタ制作を続けていました。
建築事務所では建築、インテリア、プロダクトなどのデザインを手掛けていたのですが、ニューヨークはファストファッション文化なので、モノにしてもソフトにしても、なにしろサイクル、寿命が早い。当時自分としては長く使えるものをデザインしていきたかったので、いいものはきちんと長く使う日本の文化を改めて振り返り、2011年の末に日本に帰ることにしました。
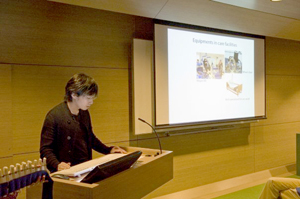
写真1:アメリカ時代の加藤氏。(クリックで拡大) |
 |
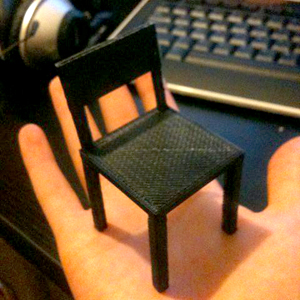
写真2:アメリカ時代、まだサポート材生成もできなかった時代の椅子のモデル。(クリックで拡大) |
●デザイナーになる予定がGENKEI設立に
--:帰国後は、日本でデザイナーを目指したわけですか?
加藤:帰国して、プロダクト、コンセプトデザイン、ブランディングなどの仕事をしたかったので、改めて就職活動用のポートフォリオを作ろうということで、再び3Dプリンタを作ることにしました。それが2012年1月頃ですが、日本には3Dプリンタ用のパーツがぜんぜんなくて、まずノズルを作るために、アルミと真鍮を削る切削工具を買ってきました(笑)。
当時、日本でRepRapで3Dプリンタを作っていたのは私を含めて数えるほどでした。そういった人たちと情報交換するために僕ともう1人と代表でRepRap Community Japanを作りました。
そして日本版のRepRapの第1号機を作ろうということで、ジョセフ・プルーシャ、Prusa Mendelを作ったりPrusai3と呼ばれる機体を作っていた今では伝説的な人ですが、プルーシャにアルミフレームの機体をリクエストしたのですが、届かなかったので、私が機体設計を担当して、もう1人の方が基板設計を行いました。それが「Atom」の第1号機となります。
最初の「Atomベータ」の機体はほぼプラスチックで構成され、組み立ては大変だけどシンプルなものでした。それを東京・お台場の日本科学未来館で行われた「Maker Faire Tokyo 2012」にプラスチックパーツだけ10セット持っていきました。アルミパーツは自分で切っていただくということを要求する時代でしたね(笑)。最初の10台のノズルは、M6のずん切りの真鍮材を使って、0.4ミリのドリルで手で空けていました。旋盤屋さんに0.4ミリの穴の加工をお願いしても、値段が折り合わなくて。それが現在に至る始まりです。
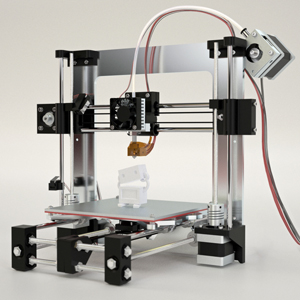
写真3:「Atom」の初代機。説明キャプション。(クリックで拡大) |
 |
|
--:Atomができてから、ポートフォリオを作ったのですか?
加藤:Maker FaireでRepRapのプレゼンテーションを行ったときにNHKの生活放送系の人が取材に来ていまして、テレビで取り上げてもらいました。そのうち民放でも3Dプリンタのメーカーとして取り上げていただいたのですが、そうなると個人では対応しきれないので、当時の友人と「GENKEI」を設立することにしました。
日本でデザイナーになるつもりが、いつの間にか3Dプリンタのメーカーを作ることになってしまったわけです(笑)。
--:テレビで放映されて、後に引けない状況になった?(笑)
加藤:テレビで紹介されてから3Dプリンタの注文も入り、ビジネスになっていったわけですが、もともとデザイナーが趣味で行っていた世界なので、会社経営もビジネスも知らなかった。「卸って何だろうがちがうんだろう」というところからですから(笑)。それでも走るしかない状況でした。
そのうちにVC,投資家のような方々から接触もあったのですが、ベンチャーのエンジェル? ファイナンス? 皆さんの真偽が分からなかったので、すべてお断りしてきました。その中でも一から教えてくださった方やいろいろな人との交渉事でそれなりに揉まれてきましたが、結局のところ、自分の目指すところは何だろう? それをずっと考えてきました。
--:GENKEI設立は、ちょうど3Dプリンタのブーム到来の時期でしたね。少し遅れてデジタルファブリケーションのブームもやってきました。
加藤:デジタルファブリケーションやメーカーズが花咲いたのは3Dプリンタの貢献が非常に大きいですね。3Dプリンタという、机上で、削りカスが出なくて、最初からプラスチックが形になって出てくる装置の登場は、一般のメディアや人々にはあまりにもインパクトが強かった。そもそもその元祖であるRP、光造形機は30年前から自動車産業などで使われているので、そのダウンサイジング版ともいえる3Dプリンタが、これほどブームになるとは、私自身考えていなかった。私の中で腑に落ちない状態が続いていました。
--:マスコミが取り上げた一般の人々のブームに違和感があったのですか?
加藤:卓上3Dプリンタの創成期から関わっている身としては普及するのはすごく嬉しいことです。atomはファームウェアなども公開しているので、それを元に別のメーカーさんが3Dプリンタを作っても何の問題もありません。電話で「製造する際、ライセンスはどうすればよいですか?」という問い合わせをいただいても「ないです」とお答えしていました(笑)。ハードウェア・オープンソースという文化が日本にそもそもなかったですからね。
RepRap系3Dプリンタの考え方は、ミニ四駆が近いかもしれませんが、ミニ四駆はタミヤさんのプラットフォーム上で様々にカスタマイズできますが、RepRapは完全にオープンなので、ここからここまでという部分すら無くオープンソースハードウェアをこれから知る人にとっては扱いに困っていたかとおもいます。
--:Atom以降、GENKEIの3Dプリンタはすべて加藤さん中心で制作していたのですか?
加藤:はい、NY時代作り続けることで電気系も分かるようになりましたし、すべての3Dプリンタの企画からデザイン、開発まですべて私が行っています。
ただ、3Dプリンタは熱が掛かって、モーター駆動部があって、押し出す内容量、素材の種類による温度、押し出しスピード、ノズルの素材、そしてサポートなど、あまりにも手間がかかりすぎるので、新規に参入する国内メーカーさんは少ないと思います。私自身も創成期に関わっていなければ、仕事にしていなかったと思います(笑)。
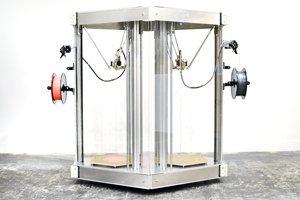
写真3:Trinoをベースとした義足専用カスタム品「Trino500Dual」。(クリックで拡大) |
 |
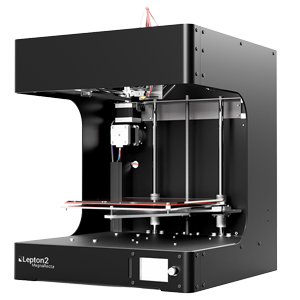
写真4:「Lepton」の最新モデル。(クリックで拡大) |
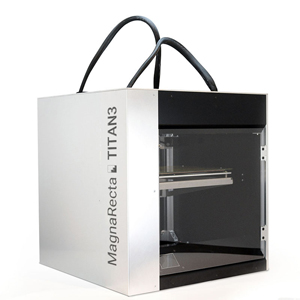
写真3:「TITAN」の最新モデル。(クリックで拡大) |
 |
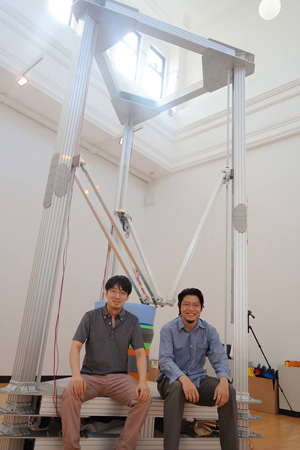
写真4:東京藝術大学藤崎研究室の櫻井稔氏と共同開発した「MAGNA」。(クリックで拡大) |
●「GENKEI」から「MagnaRecta」へ。
--:GENKEI設立から6年目で組織一新です。そのお考えを聞かせてください。
加藤:まず最初の会社名の「GENKEI」ですが、これはモノの形としての原型を指しているのではなくて、人のアイデアの原型を意味しています。私はアイデアが一番面白くて好きなんですよ。例えばクルマのデザインは好きなんですけれど、中でもコンセプトカーが特に好きです。コンセプトカー、コンセプトデザインにはフィジビリティや現実性より、エッジの尖った、作り手のアイデアの原型を見ることができます。
実際、ユーザーさんによってRepRap系3Dプリンタが出力する形状は、今では全部そうではなくなりましたが、たぶん試作用で、アイデアやプロトタイプの出力用なんですよ。
--:GENKEIは形ではなくアイデアを指していたわけですね。
加藤:はい、そして「MagnaRecta」に組織変更したのは、「GENKEI」が3Dプリンタのメーカーになってしまったからなんですね(笑)。でも私としては、アイデアを培うための機械を作っているだけなんです。あくまで3Dプリンタはアイデアの原型を作るための装置。「GENKEI」という社名はそういう意味でよかったのかなと思っています。
3Dプリンタを作っていると、実はレーザカッターも切削機も作ることができるんです。これまでGENKEIで作ってきたFDM(熱溶融式)/FFT方式の3Dプリンタの基本はロボットなんです。3軸のロボットアーム。
一方、3Dプリンティング、印刷という言葉において、DLP方式やレーザー方式の光造形機はまさに印刷機なんですね。つまりFDM方式はロボット、光造形方式は印刷機という認識を持っています。根本的に違うはずなんです。
ロボットをやっていると基本的には何でも作れます。それは幸運だったと思います。モビリティを作ることもできますし、DCモーター、ステッピングモーターなどで制御系も作れる。電圧、温度センサーなど、3Dプリンタの構成要素はロボット的であるために、応用が利くわけです。ハードメーカーとしてはいろいろ対応できる力はついたと思います。
--:MagnaRectaはハードメーカーの枠を超えたい?
加藤:「MagnaRecta」では、人のアイデアをハードウェアでどう具現化するかを考えたい。モノとコトを両方行う。ソフトだけだといわゆるコンサルティングになりますが、それはダイエット、合理化の提案になりがちです。
今、日本に欠けているのは、世の中で何が求められているのか、どう提案していくか、だと思うのです。それを言葉だけではなくモノ・サービスとして具体的に作りましょうという活動を行いたい。
日本人の思想、一般生活に余裕がない。受け身体質であるがゆえに、すべての動作がタスク化される。飲み会もタスク化または営利化(笑)。タスク処理をしてから自分の時間。他のことが入る余地がない。モノ作り文化が育たない。新しいものに対して積極的になれない。ですので、これからはアウトプットの前の失われた着想の仕方と作り方をお手伝いしたい。
例えばモビリティを作りたいという企業さんがあれば、それは1輪車なのか2輪車なのか、それともまったく別の形態なのか? その発想、アイデア段階から一緒にやりましょう。何かを作るにしても、二酸化炭素排出量や社会に落とし込んだ時の影響力まで考慮した上で新しいモノを一緒に作っていくアプローチを、もう少し日本で育てたい。
もともと大学時代からそういう発想を行ってきているので、ゼロから1を立ち上げるお手伝いしたい。
ーー:それは業種でいうと、コンサルティングというより、デザイナーの本来の仕事なのかもしれませんね。
加藤:そうですね。企業に眠る文化や技術で新しい何かを作るためのお手伝い。それはアドバイザーとも言えますし、ディレクション、ビーコンも含めたデザイナーともいえるかもしれない。
姿形という意味のデザインだけではなくて、着想の仕方からお手伝いしたい。新しいことをしたいという熱さえあれば、そこからアウトプットまで一緒に作る、そういったモノ作りの文化を日本で育てたい。
アメリカでは同時多発的に新しいものを生み出すための手助けをしている方々は会社としてもいますし、新しいものを運用手助けする環境と失敗しても問題視せず次に行けるビジネス文化があります。日本はあまりそういうことはない。
--:GENKEIからMagnaRectaへは、加藤さんの本来の資質、目的に近づくということに感じます。
加藤:これまで3Dプリンタで時代に貢献できたと思いますが、本来私の目指すところにおいてはハードだけでは実現できない。3Dプリンタの納品をきっかけに、クライアントのお話を聞く上で、ハードだけでは解決できない問題を常々感じています。
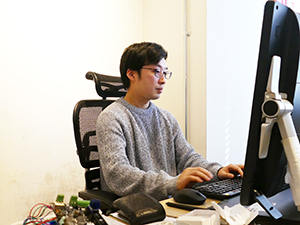
写真5:東京タワーが近い、東麻布にあるMagnaRectaのオフィスで話を聞いた。 |
 |
|
●MagnaRectaの今後の展開
--:ハードウェアの販売は今後も継続ですか?
加藤:もちろんです。3Dプリンタに関しては、LeptonやTITANに続く、次期主力も開発中です。また弊社には特注のお客様も多く、実は光造形機もレーザーカッターも受注しています。例えば義足用の3Dプリンタのオーダーがあれば、それにカスタマイズした3Dプリンタも納品しています。建築用途にもカスタマイズ製品を納品しています。新しい材料の出力もいろいろ検討しています。
カスタマイズ系を廉価でご提供できるのがMagnaRectaの強みかもしれません。多様な業種のお客様のリクエストに対応しています。ビジネス的にもカスタマイズ系の受注案件の方が大きいです。
--:カスタマイズ納品は確かに大きなアドバンテージですね。国内で競合するメーカーはないのですか? そういう点では、一番クライアントニーズに沿えるメーカーですね。
加藤:そうですね。今もレーザーカッターを受注しているのですが、置く場所がかなり特殊でそれに合わせた機体を作製していますがそれに対応できるのは弊社くらいだと思います。私はインテリア、施工も分かるので、石膏ボードや排出口、配線配管をどうするかなど、アメリカの建築事務所で働いていたスキルが生きてきます。スペックではなく運用方法優先のオーダーもお任せください(笑)。
--:ちなみに現在のメインユーザーはどういった方でしょう?
加藤:MagnaRectaはビジネス的にはB to Bメインですが、Cユーザー、ホビーユーザーも実はBだと思っています。3Dプリンタを使いこなす時点で、それはプロスキルですから、ワンフェス出ている時点でBだと思っています(笑)。どの方もモノを作る方であれば隔てなく臨む姿勢です。
--:3Dプリンタの役割がプロトタイプ制作やホビーベースより、むしろ製品出力、産業用途にシフトしているようにも感じます。そういった時代の変化に、MagnaRectaはどのように対応されますか。
加藤:月並みな言い方ですが、3Dプリンタの方式や材料は、適材適所になるでしょう。大量生産を行う金型も3Dプリンタも私の中では同質です。物理的な動作が異なるだけです。産業において3Dプリンタは伸びるでしょう。
FDM方式や光造形、金属などさまざまな出力方式がありますが、いずれも続いて成長、進化していくと思います。これから何が求められるかにどう対応するかを把握しないと、資本力に勝るメーカーが強いでしょうが、次に何が来るかを分かっている人がいるかいないかが一番のポイントだと思います。MagnaRectaでは次に何が来るかを一緒に考えて作りたい。
--:3Dプリンタも金型に代わる大量製品用途と、デジタルファブリケーション的な手作り感覚の多品種小ロット対応になってくるのかもしれませんね。
加藤:それプラス、手作業ですね。工芸品も含め3Dプリンタの用途はかなり広いと思います。
--:例えば製品クオリティで、食品も含めたどんな材料も出力できる。そういったオールマイティなデスクトップ3Dプリンタは将来ありえますか? また加藤さんの理想の3Dプリンタとは。
加藤:実際にフード3Dプリンタやガラス出力などの特殊出力の製作、共同研究などをしていますが、私が欲しいとしたら、すべてのファンクションを1つにごちゃまぜにしなくてもいいかなと思います。機体の中にいろいろ入れてもメインテナンスが大変ですし、一番いいのは機能がしっかりしているかどうか。メンテナンスがしっかりしていて、個々が使用するのにおっくうにならない3Dプリンタがあれば嬉しいかな。
--:最後に読者に向けて一言お願いします。
加藤:ゼロから何かを作りたいときは、一声かけてくださると嬉しいです。
ーー:ありがとうございました。
(2018年4月3日更新)
|